Exploring Tungsten Carbide Bushings
In the vast landscape of modern industrial manufacturing, precision mechanical components are like the crucial gears in a sophisticated instrument. Though small, they play a decisive role. Among numerous precision […]
In the vast landscape of modern industrial manufacturing, precision mechanical components are like the crucial gears in a sophisticated instrument. Though small, they play a decisive role. Among numerous precision components, tungsten carbide bushings have attracted significant attention in the industry due to their unique physical properties and an extremely wide range of applications, becoming a “star” in the industrial field. This article will conduct an in-depth analysis of the applications of tungsten carbide bushings to help readers gain a comprehensive understanding of this important mechanical component.
1. Tungsten Carbide Bushings: A Masterpiece of High-Performance Alloys
Tungsten carbide bushings, also known as cemented carbide bushings, are high-performance alloy materials meticulously crafted through powder metallurgy processes using hard compounds of refractory metals and bonding metals. This unique manufacturing process enables the perfect fusion of the high hardness of tungsten and the toughness of steel.
Our factory business: carbide parts, mold parts, medical injection molds, precision injection molds, teflon PFA injection molding, PFA tube fittings. email: [email protected],whatsapp:+8613302615729.
It’s like a martial arts master who possesses both formidable strength and flexibility. In terms of wear resistance, it is as if it is clad in an impenetrable armor, effectively resisting external wear. Regarding impact resistance, when faced with powerful impact forces, it remains as steady as a mountain. Its corrosion resistance is also remarkable; even in harsh corrosive environments, it can remain unscathed. And when it comes to high-temperature stability, it excels even further. Even under the “scorching test” of high temperatures, it can still maintain high hardness and wear resistance, a feat that many other materials can hardly match.
2. Stamping Dies: The Main Battlefield for Tungsten Carbide Bushings
In the field of stamping dies, tungsten carbide bushings are the cornerstone. Stamping dies, as the “magic tools” for manufacturing metal parts in industrial production, have tungsten carbide bushings as their vital “magic components.”
With their excellent wear resistance and impact resistance, they are like loyal guardians, silently protecting the dies, effectively extending the service life of the dies and significantly improving production efficiency. Moreover, their high surface finish is like a smooth ice surface, which can significantly reduce friction resistance during the stamping process, elevating product quality to a new level. During high-speed stamping, when facing huge impact forces, they rely on their tough “bodies” to maintain the stability and precision of the dies, ensuring that the stamped parts are precisely dimensioned and have a smooth surface like a mirror.
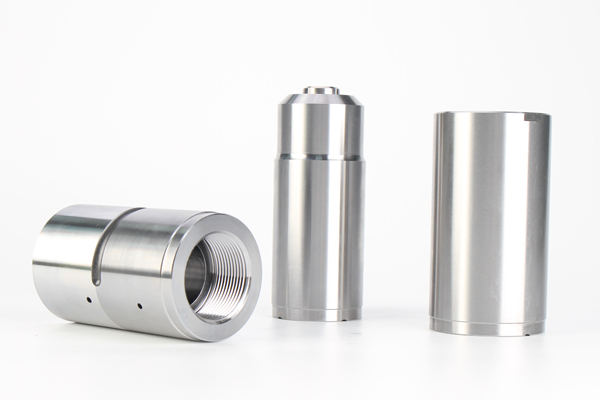
3. Drawing Processes: The Assisting Partners of Tungsten Carbide Bushings
Besides stamping dies, the drawing process is also a stage where tungsten carbide bushings can fully demonstrate their capabilities. During the drawing process of metal materials, they are like experienced commanders, calmly coping with the harsh environments of high temperatures and high pressures, ensuring the stable and precise operation of the drawing dies. This is undoubtedly a “reassuring pill” for the production of high-precision and high-quality metal products.
Especially in the drawing processes of copper parts, stainless steel parts, and other materials, due to frequent use, a large amount of heat and wear are easily generated. Tungsten carbide bushings, with their excellent wear resistance and thermal stability, are like magical “cooling agents” and “repairers,” effectively reducing die wear and heat accumulation, making the drawing process more stable and efficient.
4. Petroleum Machinery: The Tough Guardians of Tungsten Carbide Bushings
With the continuous advancement of petroleum extraction technology, more stringent requirements have been placed on the wear resistance and corrosion resistance of petroleum machinery and equipment. At this time, tungsten carbide bushings, relying on their outstanding physical properties, have stepped forward and become the “capable assistants” in petroleum machinery.
They can serve as bushings for key components such as oil well drill bits and pump bodies, providing a sturdy “protective suit” for the equipment and improving the wear resistance and service life of the equipment. In the arduous journey of petroleum extraction, they can withstand extreme working environments and harsh geological conditions, like fearless warriors, ensuring the stable operation of petroleum machinery and equipment and making significant contributions to improving petroleum extraction efficiency and reducing maintenance costs.
5. Development Path: Opportunities and Challenges Coexist
The wave of rapid technological development and industrial progress has brought broader development space for tungsten carbide bushings. In the future, they are expected to shine brightly in high-end fields such as aerospace, automotive manufacturing, and electronic information, opening a new and glorious chapter.
However, the road to development is not smooth. On the one hand, the progress of material science has led to the emergence of a large number of new high-performance materials like bamboo shoots after a rain, bringing fierce competitive pressure to tungsten carbide bushings. On the other hand, their complex manufacturing process and high cost are like heavy shackles, limiting their applications in some fields. Therefore, reducing production costs and improving production efficiency have become urgent issues that the tungsten carbide bushing industry needs to address.
6. Conclusion
In conclusion, tungsten carbide bushings play a pivotal role in the field of industrial manufacturing with their unique charm and powerful strength. In the future, with continuous technological innovation and growing market demand, they will undoubtedly embrace broader application prospects and achieve higher development levels. At the same time, the industry should also bravely face challenges, actively optimize production processes, and reduce costs to propel the tungsten carbide bushing industry towards an even more brilliant future.