How to Improving the Wear Resistance of Tungsten Carbide
In the precise operations of mechanical processing, the arduous tasks of mining, and the deep – sea explorations of oil drilling, tungsten carbide stands out as an indispensable key material […]
In the precise operations of mechanical processing, the arduous tasks of mining, and the deep – sea explorations of oil drilling, tungsten carbide stands out as an indispensable key material due to its high hardness, high strength, and excellent wear resistance. However, in real – world applications, the wear resistance of tungsten carbide is like the “sharp edge” that determines success or failure, directly related to its service life and performance. Once the wear resistance is poor, tools are prone to wear, have a shortened lifespan, which not only increases production costs but also reduces work efficiency and disrupts the smooth progress of the entire production process. Therefore, enhancing the wear resistance of tungsten carbide is of crucial importance for extending tool life, improving production efficiency, and strengthening industry competitiveness. Next, this article will comprehensively and in – depth explore effective methods for improving the wear resistance of tungsten carbide, providing practical references for relevant industries.
I. Optimize Material Composition to Lay a Solid Foundation for Wear Resistance
The wear resistance of tungsten carbide is closely linked to its composition, just as the foundation of a building determines its stability. By carefully optimizing the alloy composition, its wear resistance can be effectively improved.
Our factory business: carbide parts, mold parts, medical injection molds, precision injection molds, teflon PFA injection molding, PFA tube fittings. email: [email protected],whatsapp:+8613302615729.
- Precisely Adjust the Ratio of Tungsten Carbide and Binder: Tungsten carbide, as the main component of the alloy, is like the “hard skeleton”, endowing the alloy with high hardness. The binder (such as cobalt, nickel, etc.) is like the “flexible joint”, enhancing the alloy’s toughness and strength. By skillfully adjusting the ratio of these two, it is like finding a perfect balance between hardness and toughness, enabling the alloy to have sufficient hardness to resist wear while possessing good toughness to prevent fracture, thus significantly improving wear resistance.
- Cleverly Add Other Alloying Elements: Introducing elements such as tantalum and niobium is like casting a “refining spell” for the alloy, which can refine the grains, make the alloy structure more dense and uniform, and thereby increase hardness and wear resistance. Adding elements like chromium and vanadium is like putting on a “protective armor” for the alloy, improving its oxidation resistance and corrosion resistance, reducing the erosion of external factors on the alloy, and indirectly enhancing wear resistance.
II. Innovate Preparation Processes to Forge Excellent Performance
In addition to optimizing the material composition, improving the preparation process is also an important “magic weapon” for enhancing the wear resistance of tungsten carbide.
- Employ Powder Metallurgy Technology: Powder metallurgy technology is like a skilled “craftsman” who can precisely control the composition and microstructure of the alloy, creating tungsten carbide with high density and excellent performance. By carefully optimizing process parameters such as powder particle size, pressing pressure, and sintering temperature, it is like providing the “craftsman” with more precise tools, further improving the alloy’s wear resistance.
- Introduce Heat Treatment Processes: Heat treatment is like a process of “internal remodeling” for tungsten carbide. Through quenching and tempering treatments, residual stresses inside the alloy can be eliminated, similar to relaxing tense muscles, improving toughness and wear resistance. At the same time, using surface treatment techniques such as carburizing and nitriding is like adding a “hard outer layer” to the alloy surface, enhancing surface hardness and wear resistance.
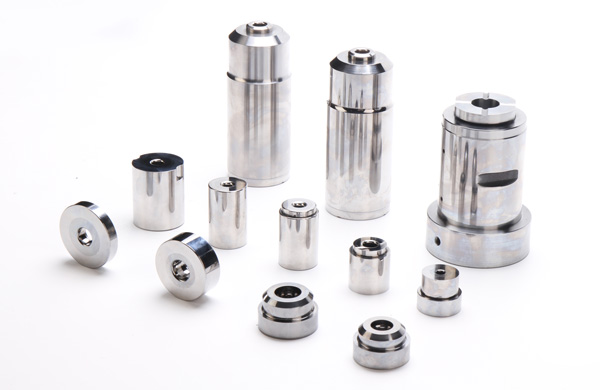
III. Optimize Usage Conditions to Create a Favorable Environment
The wear resistance of tungsten carbide is not only determined by the material itself but is also closely related to usage conditions. Optimizing usage conditions can create a good “working environment” for tungsten carbide, thereby improving its wear resistance.
- Reasonably Select Cutting Parameters: In mechanical processing, the selection of cutting speed, feed rate, and cutting depth is like setting the “movement rhythm” for tungsten carbide tools. According to the specific processing materials and process requirements, these parameters should be reasonably adjusted to avoid excessive loads on the tools and reduce the wear rate.
- Strengthen Cooling and Lubrication: The heat and friction generated during cutting are like “wear catalysts” that accelerate the wear of tungsten carbide. Therefore, strengthening cooling and lubrication is crucial. Using efficient coolants and lubricants is like providing a “cool protective shield” for the tools, reducing the cutting temperature and friction, and extending the tool service life.
IV. Conduct Regular Maintenance to Prolong Tool Vitality
During use, tungsten carbide tools, like hard – working laborers, require regular maintenance and upkeep to maintain good working conditions and wear resistance.
- Regularly Clean the Tool Surface: The chips and dirt on the tool surface are like “hidden enemies” that can cause secondary wear to the tools. Regularly cleaning these impurities is like “sweeping away obstacles” for the tools, keeping their surfaces clean and smooth.
- Regularly Inspect Tool Wear: Timely understanding of tool wear is like conducting a “health check – up” for the tools. Once severely worn or damaged tools are detected, they should be replaced immediately to avoid affecting processing quality and efficiency due to tool problems.
- Regularly Apply Coating Treatments: Regular coating treatments for tools are like dressing them in “wear – resistant battle suits”. Using techniques such as physical vapor deposition (PVD) or chemical vapor deposition (CVD) to form a hard coating on the tool surface can significantly enhance its surface hardness and wear resistance.
V. Develop New Materials to Open Up the Future Path
With the rapid development of science and technology, developing new tungsten carbide materials has become an effective way to improve wear resistance. By introducing new alloying elements and adopting advanced preparation processes, it is like opening a “door of innovation” for tungsten carbide, enabling the development of new tungsten carbide materials with more excellent performance. These new materials not only have higher hardness and wear resistance but may also possess better oxidation resistance, corrosion resistance, and other characteristics, meeting the needs of more demanding working environments and bringing new opportunities and challenges to relevant industries.
VI. Summary and Outlook
Improving the wear resistance of tungsten carbide is a systematic project that involves multiple aspects such as material composition optimization, preparation process improvement, usage condition optimization, regular maintenance, and new material development. Only by comprehensively considering these factors can a practical improvement plan be formulated, allowing tungsten carbide to play a greater role in various fields. With the continuous emergence of new materials and processes and the rapid development of intelligent manufacturing technology, we have reason to believe that the wear resistance of tungsten carbide will be further improved in the future, injecting new vitality into the development of relevant industries. At the same time, we should also pay attention to the environmental performance of tungsten carbide, promote green manufacturing and sustainable development, and contribute to building a resource – saving and environment – friendly society. Let’s work together to explore a new journey of improving the wear resistance of tungsten carbide and create a better future!
Related Posts
- Revelation of the Processing Specifications of Tungsten Carbide Drawing Dies
- How to use tungsten carbide to process efficiency and extend tool life
- Key Points to Note in the Cracking Process of Tungsten Carbide Tool Grinding
- Maintenance Secrets of Tungsten Carbide Blades: A Comprehensive Guide to Prolonging Lifespan and Enhancing Performance