Maintenance Secrets of Tungsten Carbide Blades: A Comprehensive Guide to Prolonging Lifespan and Enhancing Performance
In numerous fields such as mechanical processing and mold manufacturing, tungsten carbide blades have become indispensable “capable assistants” due to their high hardness, excellent wear resistance, and outstanding cutting performance. […]
In numerous fields such as mechanical processing and mold manufacturing, tungsten carbide blades have become indispensable “capable assistants” due to their high hardness, excellent wear resistance, and outstanding cutting performance. However, similar to how even the sharpest sword requires meticulous care, tungsten carbide blades also face challenges of wear and damage during use. Proper maintenance methods can not only extend the service life of the blades but also enable them to consistently maintain superior cutting performance, safeguarding production efficiency and product quality. Next, let’s delve into the maintenance methods for tungsten carbide blades.
Daily Cleaning and Drying: Attention to Detail Matters
After each use of tungsten carbide blades, cleaning should never be overlooked. Imagine that cutting chips, oil stains, and other impurities are like “little devils” lurking on the blade surface. If not cleaned promptly, they will gradually erode the blade’s performance. At this time, we can use clean water, a soft cloth, or a brush to gently wipe the blade surface and remove these “little devils.” However, it is crucial to remember that hard objects or sharp tools are the “enemies” of the blades. Never use them for cleaning; otherwise, a single careless move may leave scratches on the blade surface, affecting its cutting accuracy.
Our factory business: carbide parts, mold parts, medical injection molds, precision injection molds, teflon PFA injection molding, PFA tube fittings. email: [email protected],whatsapp:+8613302615729.
After cleaning, keeping the blade dry is equally important. Water residue is like a “time bomb” that can trigger the risk of blade rusting at any time. We can dry the blade with a clean cloth or use a hairdryer to blow it dry. In addition, the choice of storage environment is also vital. A dry and well-ventilated place is the “ideal home” for tungsten carbide blades, which can prevent damage caused by moisture and corrosive gases. If conditions permit, placing desiccants in the box or cabinet where the blades are stored is like putting up an “umbrella” for the blades, effectively absorbing moisture in the air and maintaining a dry environment.
Regular Sharpening and Oil Application: Infusing “Vitality” into the Blades
As the usage time increases, tungsten carbide blades will gradually become dull, just like a rusty sword that has lost its former sharpness. At this point, regular sharpening becomes particularly crucial. Sharpening is a technical task that requires the use of professional sharpening stones or sharpeners and strict adherence to the correct angle and force during the process. Over-sharpening is like putting the blades on an “excessive diet,” which can damage the hard coating on the blade surface and reduce its service life. Therefore, it is essential to strike a balance during sharpening to restore the blade’s sharpness while maintaining its original performance.
After sharpening, applying a layer of professional cutting tool oil or lubricant to the blade is like putting on a “protective suit.” We can use a wiping cloth or the immersion coating method to allow the blade to absorb a small amount of oil, maintaining its surface smoothness and preventing corrosion. Moreover, the oil can form a lubricating film between the blade and the cutting material, reducing friction and slowing down the blade’s wear rate, making the cutting process smoother.
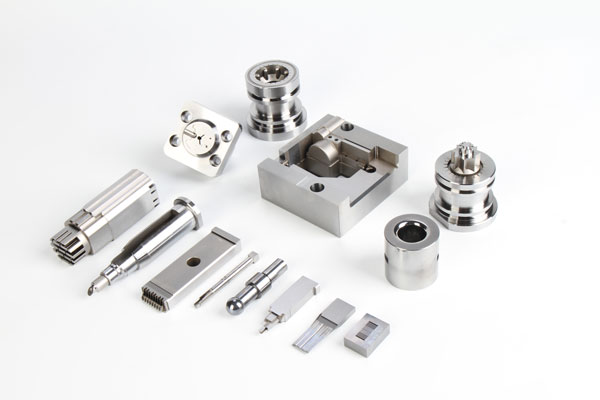
Proper Use and Avoidance of Collisions: Gentle Treatment is Key
When using tungsten carbide blades, strictly following the operating procedures is a fundamental principle. Just as driving a car requires obeying traffic rules, we should avoid overusing the blades on hard materials or performing inappropriate cutting operations; otherwise, the blades are prone to “injury.” At the same time, we should remain vigilant during use and handle the blades with care to prevent collisions or friction with other hard objects. A single inadvertent collision may cause cracks or chipping on the blade, affecting its normal use.
When installing and removing the blades, extra caution is required. Using specialized tools for operation is like providing the blades with an exclusive key, ensuring the safety and accuracy of the installation and removal process. Avoid applying excessive force or improper operations to prevent blade deformation or damage. During installation, it is also necessary to ensure a tight and secure fit between the blade and the blade holder, just like fitting pieces of a puzzle perfectly, to prevent looseness or detachment during use and avoid unnecessary production disruptions.
Regular Inspection and Replacement: Prevention is Better than Cure
To ensure that tungsten carbide blades are always in optimal performance condition, regular inspection is an indispensable step. Just as a doctor conducts regular physical examinations for patients, we should carefully observe whether the blades have cracks, chipping, or wear. Once these problems are detected, like discovering minor health issues, timely treatment or replacement of new blades should be carried out to prevent the problems from worsening and affecting production.
At the same time, it is also crucial to reasonably formulate the blade replacement cycle based on factors such as usage conditions and the hardness of the cutting material. Generally, when the cutting performance of the blades significantly declines or severe wear occurs, it means they are “exhausted” and need to be replaced with new ones to continue “serving” in production.
Professional Maintenance and Care: Tailored Protection
For tungsten carbide blades on large-scale mechanical equipment or high-precision processing equipment, regular professional maintenance and care are essential to ensure their stable performance. We can invite professional technicians to conduct comprehensive inspections, adjustments, and repairs on the equipment, just like giving the equipment a comprehensive “health check,” to keep the blades in the best working condition.
In addition, different types of tungsten carbide blades and processing requirements are like different people having different preferences, necessitating the formulation of personalized maintenance plans. For example, for equipment that requires continuous long-term operation, we can take measures such as regular shutdown cooling, cleaning, and lubrication, just like giving the equipment a “break” to allow it to receive sufficient rest and maintenance, thereby extending the service life of the blades. For blades on high-precision processing equipment, more attention should be paid to cleaning and precision adjustment during maintenance, just like fine-tuning precision instruments to ensure their processing accuracy and product quality.
The maintenance of tungsten carbide blades is a systematic project, covering daily cleaning and drying, regular sharpening and oil application, proper use and avoidance of collisions, regular inspection and replacement, as well as professional maintenance and care. As long as we take good care of them with scientific and reasonable maintenance measures, we can enable tungsten carbide blades to always maintain their best condition, providing strong support for our production work. At the same time, it can also reduce production costs, improve production efficiency, and help us stand out in the fierce market competition.