Key Points to Note in the Cracking Process of Tungsten Carbide Tool Grinding
In the vast realm of machining, tungsten carbide tools are like a set of “sharp blades”. With their high hardness, high strength, and excellent wear resistance, they shine brightly in […]
In the vast realm of machining, tungsten carbide tools are like a set of “sharp blades”. With their high hardness, high strength, and excellent wear resistance, they shine brightly in various machining scenarios and become indispensable assistants for many practitioners. However, during the grinding process of tungsten carbide tools, the issue of cracks is like a “time bomb”, constantly threatening the service life of the tools, machining quality, and operational safety. Once cracks appear, the tools may be scrapped prematurely, machining accuracy may be significantly compromised, and even safety accidents may occur. Therefore, when grinding tungsten carbide tools, it is essential to attach great importance to and strictly control several key issues to fully prevent the occurrence of cracks.
Grinding Wheel Selection: Precise Matching to Avoid Risks
The selection of the grinding wheel is of utmost importance when grinding tungsten carbide tools. Since tungsten carbide materials have extremely high hardness and considerable brittleness, they are like a piece of hard yet fragile “glass”. If a grinding wheel with an excessively coarse grain size or high hardness is used, the grinding process will be akin to vigorously rubbing glass with rough sandpaper, easily generating excessive heat and stress, and greatly increasing the risk of crack formation. Therefore, a grinding wheel with a fine grain size and moderate hardness should be selected. At the same time, the rotational speed and feed rate of the grinding wheel should be reasonably controlled to avoid over-grinding and heat accumulation, thus laying a solid first line of defense for tool grinding.
Nuestra actividad de fábrica: piezas de carburo, piezas de molde, moldes de inyección médica, moldes de inyección de precisión, moldeo por inyección de teflón PFA, accesorios de tubo PFA. correo electrónico: [email protected],whatsapp:+8613302615729.
Temperature Control: Cooling and Temperature Reduction to Suppress Cracks
Tungsten carbide materials are prone to generating high temperatures during grinding, just like being placed on a fire. And high temperature is one of the main culprits leading to crack formation. Therefore, during the grinding process, the grinding temperature must be strictly controlled, just as we cool down a feverish patient. On the one hand, the grinding temperature can be reduced by cleverly adjusting the rotational speed and feed rate of the grinding wheel. On the other hand, sufficient cooling fluid should be used to continuously cool the grinding area, like giving a high-temperature tool a “cold shower”, reducing heat accumulation and temperature gradients, thereby effectively lowering the risk of crack formation.
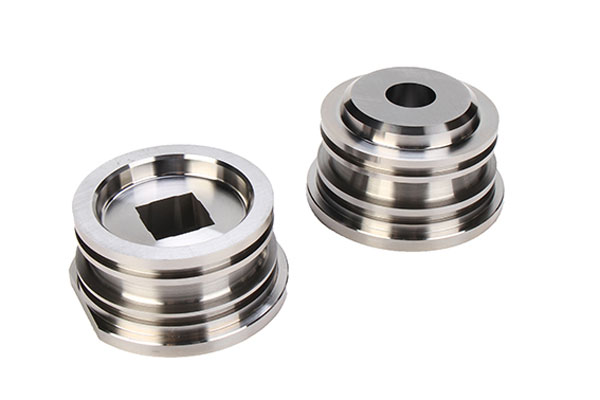
Stable Grinding Force: Even Application for Smooth Machining
Unstable grinding force is also an accomplice in causing cracks. During the grinding process, if the grinding force suddenly increases or decreases, it will be like suddenly stepping on the accelerator or brake of a moving car, subjecting the tool to huge impacts and easily leading to crack formation. Therefore, the grinding force should be kept stable by adjusting the rotational speed, feed rate, and grinding depth of the grinding wheel. At the same time, operators should be like experienced drivers, possessing rich experience and superb skills, and be able to flexibly adjust the grinding parameters according to actual conditions to ensure a smooth grinding process.
Proper Clamping: Firm and Appropriate to Reduce Stress
The clamping method of tungsten carbide tools during the grinding process has a significant impact on the stress and crack formation of the tools. The tools should be firmly clamped on the grinder, just like carefully protecting a precious item, ensuring that they do not shake or shift during the grinding process. At the same time, the clamping force should be just right, neither too tight to cause tool deformation nor too loose to make the tools vibrate during grinding. A proper clamping method is like putting on a “protective suit” for the tools, effectively reducing the risk of crack formation.
Equipment Maintenance: Regular Inspection to Ensure Precision
The precision and stability of the grinder play a decisive role in the grinding quality of tungsten carbide tools. Just as a car needs regular maintenance, the grinder should also be regularly inspected and maintained to ensure it is in good working condition. The inspection items include the balance of the grinding wheel, the precision of the spindle, and the flatness of the guide rails. Once any problems are found, they should be adjusted and repaired in a timely manner to avoid crack problems caused by equipment failures and provide reliable hardware support for tool grinding.
Technological Innovation: Advanced Assistance to Improve Quality
With the rapid development of technology, more and more advanced grinding technologies have emerged like bamboo shoots after a rain and have been widely applied in the processing of tungsten carbide tools. For example, using CNC grinders for precise control is like equipping the grinding process with an “intelligent brain”, enabling high-precision machining; using superhard abrasive grinding wheels improves grinding efficiency and quality, like installing an “accelerator” for tool grinding; applying online monitoring systems to monitor the grinding process in real-time can promptly detect and solve problems, like having a pair of “sharp eyes” for the grinding process. The application of these advanced technologies can effectively reduce the risk of crack formation and improve the service life and machining quality of the tools.
Personnel Enhancement: Training and Assessment to Strengthen Skills
Finally, but equally importantly, is the skill and experience of the operators. Grinding tungsten carbide tools is a highly technical task that requires operators to have rich practical experience and superb operational skills, just like a highly skilled craftsman. Enterprises should regularly train and assess operators to ensure they have a thorough mastery of grinding processes and techniques and can flexibly adjust grinding parameters according to actual conditions, thereby effectively reducing the risk of crack formation.
In conclusion, in the cracking process of tungsten carbide tool grinding, several aspects must be paid attention to, including selecting the appropriate grinding wheel, controlling the grinding temperature and cooling, maintaining a stable grinding force, paying attention to the tool clamping method, regularly inspecting and maintaining the grinder, adopting advanced grinding technologies, and improving the skills and experience of operators. Only by focusing on these issues and taking corresponding measures can the risk of crack formation during the grinding process of tungsten carbide tools be effectively reduced, enabling the tools to play a greater role in machining and creating higher value for enterprises.