Unlock the “Long-Lasting” Secret of Tungsten Carbide
In the grand industrial landscape, tungsten carbide shines like a dazzling star. With its extraordinary hardness, exceptional wear resistance, and outstanding high-temperature performance, it plays an irreplaceable role in numerous […]
In the grand industrial landscape, tungsten carbide shines like a dazzling star. With its extraordinary hardness, exceptional wear resistance, and outstanding high-temperature performance, it plays an irreplaceable role in numerous key fields. Whether it’s precision mechanical processing, high-intensity mining operations, or the advanced aerospace sector, tungsten carbide can be seen making remarkable contributions.
However, just as even the mightiest warrior has his vulnerabilities, tungsten carbide, as a high-performance material, also has several aspects that require attention during use. Only by fully recognizing and adhering to these precautions can we maximize the performance of tungsten carbide and effectively extend its service life. Next, let’s delve into the key factors that must be considered when using tungsten carbide.
Nuestra actividad de fábrica: piezas de carburo, piezas de molde, moldes de inyección médica, moldes de inyección de precisión, moldeo por inyección de teflón PFA, accesorios de tubo PFA. correo electrónico: [email protected],whatsapp:+8613302615729.
I. In-Depth Understanding of Material Characteristics for Better Utilization
Before putting tungsten carbide into use, it is crucial to have a comprehensive and in-depth understanding of its material characteristics. Tungsten carbide is an alloy material crafted through powder metallurgy by combining hard compounds of refractory metals with binder metals. It is like a versatile “all-rounder,” possessing high hardness, excellent wear resistance, high strength, and good toughness.
But don’t be deceived by its formidable appearance; tungsten carbide is not invincible. It has a certain degree of brittleness, similar to a seemingly unbreakable glass that can still shatter under excessive impact and bending forces. Therefore, during use, it is essential to avoid subjecting it to excessive impact and bending to prevent material fracture and ensure normal operation.
II. Precise Selection of the Right Type for Optimal Performance
Tungsten carbide comes in a wide variety of types, each like an athlete with unique strengths, having its own distinct performance and applicable scenarios. When selecting tungsten carbide, it is necessary to carefully choose the most suitable material based on the specific application scenario and working conditions.
For instance, when manufacturing cutting tools that require high hardness and wear resistance, tungsten carbide with a high proportion of tungsten carbide (WC) should be the top choice. WC acts like the “sharp teeth” of the cutting tool, endowing it with powerful cutting capabilities to handle various hard materials with ease. On the other hand, for applications that need to withstand significant impact forces, such as drill bits in mining operations, tungsten carbide containing an appropriate amount of cobalt binder should be selected. The cobalt binder serves as a tough “ligament,” enhancing the toughness of tungsten carbide and preventing it from breaking under heavy impact, ensuring smooth work progress.
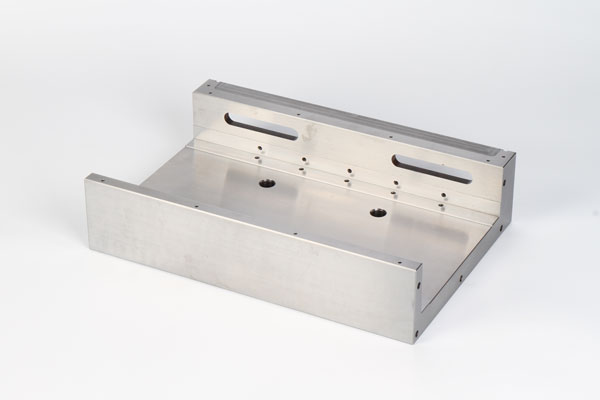
III. Standardized Use and Careful Maintenance for Prolonged Lifespan
Strict Temperature Control to Avoid Overheating Risks
Tungsten carbide is highly sensitive to temperature, much like a delicate “guest” that can lose its original hardness and wear resistance in high-temperature environments, thus affecting its working performance. Therefore, during use, especially in cutting, drilling, and other processing operations, great attention must be paid to cooling and lubrication. By implementing reasonable cooling and lubrication measures, the generation of heat can be effectively reduced, preventing tungsten carbide from “going on strike” due to overheating.
Gentle Handling to Prevent Hard Object Damage
Although tungsten carbide has relatively high hardness, it is not “impervious to all weapons.” During storage and use, it should be treated with the utmost care to avoid contact with other hard objects, just as one would handle a precious work of art. Any collision or friction with hard objects can easily scratch or notch the surface of tungsten carbide, which not only affects its appearance but also reduces its performance and service life.
Regular Cleaning to Maintain Peak Performance
Regular cleaning of tungsten carbide tools or parts is a vital step in maintaining their performance and extending their service life. Similar to how we clean our faces and brush our teeth every day, tungsten carbide needs to have attached dirt, grease, and other impurities removed. These impurities are like hidden “time bombs” on the surface of tungsten carbide. If not cleaned promptly, they may gradually erode the tungsten carbide and affect its performance. Through regular cleaning, tungsten carbide can always be kept in its best condition, providing strong support for efficient work.
Rational Setting of Cutting Parameters to Avoid Excessive Wear
When using tungsten carbide cutting tools, setting the cutting parameters is as crucial as controlling the heat in cooking. The cutting speed, feed rate, and cutting depth should be carefully selected according to the hardness and toughness of the material. If the cutting parameters are set too high, it is like putting excessive pressure on the cutting tool, which will lead to rapid wear or even damage of the tool, increasing usage costs. Therefore, rational setting of cutting parameters is the key to ensuring the efficient and stable operation of tungsten carbide cutting tools.
Regular Inspection and Timely Replacement to Prevent Problems Before They Arise
After a period of use, tungsten carbide tools, like soldiers who have traveled a long distance, are bound to show signs of wear or damage. Therefore, regular inspection of the tool’s condition is an indispensable step. Once severe wear or damage is detected, the tool should be replaced promptly to avoid affecting work progress and quality due to tool failure.
IV. Strict Adherence to Safety Operations for Personal Protection
Wearing Protective Equipment to Build a Solid Safety Barrier
When handling tungsten carbide, safety always comes first. Just as soldiers need to wear armor when going to battle, operators must wear appropriate protective equipment, such as gloves and goggles. These protective devices act as a sturdy barrier, effectively preventing flying fragments from causing harm to operators and providing strong protection for work safety.
Standardized Operating Procedures to Eliminate Violations
When using tungsten carbide tools, it is essential to strictly follow the correct operating procedures. Similar to how drivers must abide by traffic rules, operators should not attempt to stabilize or support a running tool with their hands or other body parts. Such non-compliant operations are like driving in the wrong direction on a highway, highly likely to trigger accidents and cause serious harm to oneself and others.
Ensuring Safe Storage and Transportation to Prevent Accidental Damage
The storage and transportation environment of tungsten carbide also has strict requirements. It should be stored in a dry and well-ventilated place, away from humid and corrosive environments, just as providing a comfortable “home” for tungsten carbide. During transportation, it is necessary to ensure that tungsten carbide is properly packaged and secured to prevent collisions or damage during transit and ensure its safe and intact arrival at the destination.
V. Timely Maintenance and Professional Repair to Restore Tool Performance
When tungsten carbide tools show signs of wear or damage, timely maintenance and repair are crucial for restoring their performance. For minor wear, methods such as grinding or re-sharpening can be used to restore the tool’s performance, just like sharpening a rusty knife. However, for severe damage or fractures, it may be necessary to replace new tungsten carbide components. When performing maintenance and repair, it is advisable to seek the help of professionals. Professionals are like experienced doctors who can accurately assess the degree of tool damage and adopt the correct repair methods to avoid further damage to the tool due to improper operation.
Tungsten carbide, as a high-performance material, has a broad application prospect in the industrial field. However, to fully unleash its advantages and ensure safety and efficiency during use, it is imperative to strictly adhere to the above-mentioned precautions. By gaining an in-depth understanding of material characteristics, precisely selecting the right type, standardizing use and maintenance, strictly following safety operation procedures, and promptly carrying out maintenance and repair, we can make tungsten carbide shine even more brilliantly on the industrial stage and contribute greater strength to industrial development.