The Secrets to Longevity of Tungsten Carbide Conductive Blocks
In the intricate operations of the power and electronics industries, tungsten carbide conductive blocks reign supreme as key components, thanks to their unparalleled high hardness, high strength, and excellent conductivity. […]
In the intricate operations of the power and electronics industries, tungsten carbide conductive blocks reign supreme as key components, thanks to their unparalleled high hardness, high strength, and excellent conductivity. However, even the toughest of blocks are not immune to the ravages of time, especially when operating under high-speed, high-temperature, and high-load conditions. Such environments inevitably lead to wear, which not only shortens their lifespan but also poses a hidden threat to the stable operation of equipment. Today, let’s delve into the mysteries of reducing wear on tungsten carbide conductive blocks, empowering your equipment to perform at its peak while slashing maintenance costs!
I. Unmasking the Culprits of Wear
- Frictional Wear: Every interaction during operation is a test for tungsten carbide conductive blocks. In extreme environments, frictional wear becomes an ever-present menace.
- Chemical Corrosion: In the gentle embrace of certain chemicals, tungsten carbide conductive blocks can gradually succumb, with surface materials peeling away and wear accelerating.
- Fadiga do material: Long-term exposure to alternating loads can fatigue even the toughest tungsten carbide, leading to cracks and spalling.
- Improper Installation and Maintenance: Carelessness during installation and procrastination in maintenance can act as catalysts for abnormal wear on tungsten carbide conductive blocks.
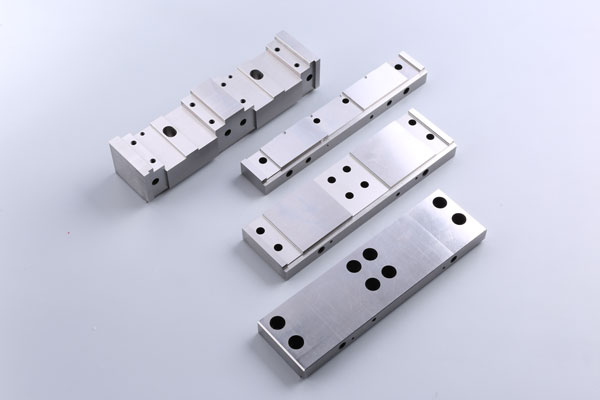
II. A Comprehensive Defense Strategy Against Wear
- Optimizing Material Selection and Treatment
- Selecting High-Quality Materials: Choose top-notch tungsten carbide materials that inherently possess high hardness, high strength, and wear resistance.
- Surface Hardening: Employ surface treatment techniques like carburizing and nitriding to fortify tungsten carbide conductive blocks with an impenetrable armor, enhancing their wear resistance.
- Improving Design Structure
- Morphological Optimization: Redesign the shape and structure of tungsten carbide conductive blocks to minimize stress concentration, rendering material fatigue untraceable.
- Gap Control: Design reasonable fit clearances to avoid overly tight or loose fits, ensuring every interaction is just right.
- Enhancing Lubrication and Cooling
- Lubricating Film Protection: Apply an appropriate amount of lubricant to friction areas, forming a lubricating film that significantly reduces the friction coefficient and, consequently, wear.
- Cooling Measures: In high-speed, high-temperature environments, install cooling devices or use coolants to keep tungsten carbide conductive blocks cool and extend their operational lifespan.
- Standardizing Installation and Maintenance Operations
- Installation Specifications: Adhere strictly to installation specifications to ensure every installation is precise and error-free, providing tungsten carbide conductive blocks with a stable home.
- Regular Inspections: Conduct regular check-ups on tungsten carbide conductive blocks to promptly detect and address issues like wear and cracks, preventing minor problems from escalating.
- Improving the Quality of the Operating Environment
- Environmental Regulation: Control humidity, temperature, and other conditions in the operating environment to create a comfortable workspace for tungsten carbide conductive blocks.
- Protective Isolation: In chemically corrosive environments, employ protective covers, isolation layers, and other measures to shield tungsten carbide conductive blocks from harm.
III. Implementation Strategies and Thoughtful Suggestions
- Formulating a Maintenance Plan: Tailor a maintenance plan based on equipment usage and the wear status of tungsten carbide conductive blocks to ensure timely detection and resolution of issues.
- Strengthening Employee Training: Provide professional training for operators to enhance their understanding of installation, maintenance, and usage specifications for tungsten carbide conductive blocks, ensuring every operation is both professional and reassuring.
- Establishing a Monitoring Mechanism: Regularly inspect, measure, and record the wear status of tungsten carbide conductive blocks to establish a monitoring mechanism that provides a solid basis for taking appropriate measures.
- Technological Innovation and R&D: Encourage enterprises to increase investment in technological R&D, exploring innovative solutions like new materials, surface treatment technologies, and design structures to further elevate the wear resistance of tungsten carbide conductive blocks.
IV. Conclusão
Reducing wear on tungsten carbide conductive blocks is no small feat; it’s a systematic endeavor that requires comprehensive consideration from material selection, design structure, lubrication and cooling, installation and maintenance, to the operating environment. By implementing the aforementioned measures and suggestions, we can effectively reduce the wear rate of tungsten carbide conductive blocks, extend their lifespan, and ensure more stable and efficient operation of equipment. Looking ahead, with the continuous emergence of new materials and technologies, we have every reason to believe that the wear resistance of tungsten carbide conductive blocks will usher in an even brighter future!
O nosso negócio de fábrica: peças de metal duro, peças de molde, moldes de injeção médica, moldes de injeção de precisão, moldagem por injeção de teflon PFA, acessórios para tubos PFA. e-mail: [email protected],whatsapp:+8613302615729.