Tungsten Carbide Bushing Processing Equipment
In the wake of the rapid advancement of modern industry, a multitude of high-precision and high-efficiency processing equipment has continuously emerged, providing robust technical support for the processing of various […]
In the wake of the rapid advancement of modern industry, a multitude of high-precision and high-efficiency processing equipment has continuously emerged, providing robust technical support for the processing of various materials. Tungsten carbide, renowned for its high hardness, strength, and wear resistance, finds extensive applications in fields such as mechanical manufacturing and mold fabrication. As a critical component within this realm, the processing quality and efficiency of tungsten carbide bushings directly impact the performance and service life of related equipment. Consequently, the research and development of efficient and precise processing equipment for tungsten carbide bushings have become of paramount importance.
I. Design Principles: The Foundation of Processing Equipment
When designing tungsten carbide bushing processing equipment, several key principles must be adhered to in order to ensure the equipment’s outstanding performance and reliability.
O nosso negócio de fábrica: peças de metal duro, peças de molde, moldes de injeção médica, moldes de injeção de precisão, moldagem por injeção de teflon PFA, acessórios para tubos PFA. e-mail: [email protected],whatsapp:+8613302615729.
High-Precision Principle: The processing accuracy of tungsten carbide bushings directly affects their operational effectiveness. Therefore, the equipment design must guarantee high precision throughout the processing, encompassing aspects such as positioning accuracy, repeat positioning accuracy, and the surface finish of the processed parts.
High-Efficiency Principle: To enhance production efficiency and reduce costs, the processing equipment should be capable of rapid and continuous operation. This necessitates stable operational performance, minimizing downtime and failure rates to ensure a seamless production flow.
Flexibility Principle: Given the diverse specifications and sizes of tungsten carbide bushings, the processing equipment should possess a certain degree of flexibility to accommodate the processing needs of different product specifications, enabling “one machine for multiple uses.”
Safety Principle: During the equipment design process, the safety of operators must be prioritized. Necessary safety protection devices and emergency shutdown systems should be incorporated to provide comprehensive safety safeguards for operators.
II. Main Components: A Matrix of Precision Collaboration
Tungsten carbide bushing processing equipment consists of several key components that work in precise coordination to accomplish high-precision processing tasks.
Machine Bed and Support Structure: As the foundation of the processing equipment, the machine bed is responsible for supporting and securing other components. It must possess sufficient rigidity and stability to provide a smooth support for the processing, ensuring that processing accuracy remains unaffected by external factors.
Spindle System: The spindle system is the core component of the processing equipment, driving the cutting tool to rotate at high speeds and complete the machining of tungsten carbide bushings. The precision and stability of the spindle directly determine the processing quality, serving as a crucial indicator of the equipment’s performance.
Feed System: The feed system is responsible for precisely controlling the movement speed and direction of the workpiece or cutting tool to achieve accurate processing trajectories. It typically comprises servo motors, ball screws, and guide rails, ensuring the accuracy and stability of the processing through precise coordination.
Tool System: The cutting tool is the component that directly contacts the workpiece. Its material, shape, and grinding quality have a pivotal impact on the processing effect. Given the high hardness of tungsten carbide, it is essential to select cutting tool materials with excellent wear resistance to ensure the tool’s service life and cutting performance during processing.
Cooling and Lubrication System: During the processing, significant amounts of heat and friction are generated between the cutting tool and the workpiece, which not only affects the processing quality but also shortens the tool’s lifespan. Therefore, an effective cooling and lubrication system is crucial to promptly reduce temperatures, minimize friction, and enhance both processing quality and tool longevity.
Control System: The control system serves as the “brain” of the processing equipment, responsible for receiving operational instructions and precisely coordinating the movement of various components. Modern processing equipment commonly employs CNC technology, utilizing advanced algorithms and programs to achieve high-precision and high-efficiency processing.
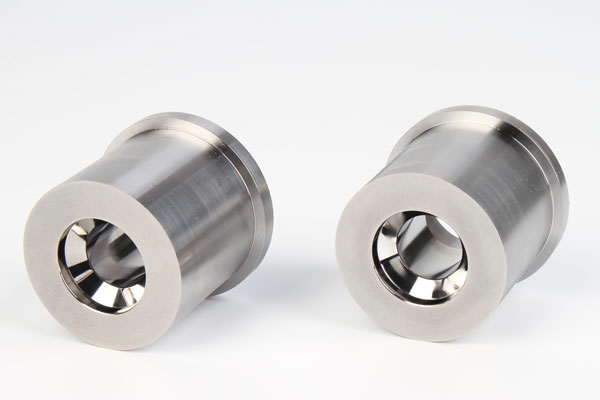
III. Workflow: A Rigorous and Orderly Processing Journey
The workflow of tungsten carbide bushing processing equipment is rigorous and orderly, with each stage interconnected to ensure the high-quality completion of processing tasks.
Workpiece Clamping: Initially, the tungsten carbide bushing to be processed is accurately and securely clamped onto the processing equipment, preparing it for subsequent processing.
Setting Processing Parameters: Based on the processing requirements, the spindle speed, feed rate, cutting depth, and other parameters are meticulously set through the control system to ensure the processing aligns with the design specifications.
Starting Processing: The processing equipment is initiated, with the spindle driving the cutting tool to rotate at high speeds while the feed system controls the movement of the workpiece or cutting tool along the predetermined trajectory, commencing the cutting process.
Monitoring and Adjustment: During the processing, the operator continuously monitors the processing status and makes real-time adjustments to the parameters or intervenes as necessary to ensure the processing remains in an optimal state.
Inspection and Finishing: Upon completion of the processing, the tungsten carbide bushing undergoes rigorous quality inspection. If any quality issues are detected, prompt finishing or rework is carried out to ensure the product meets the quality standards.
Unloading and Cleaning: Finally, the processed tungsten carbide bushing is removed from the equipment, and the equipment is thoroughly cleaned and maintained to prepare it for the next processing cycle.
IV. Development Trends: Pioneering New Directions for the Industry
With the continuous advancement of technology and the increasing level of industrial automation, tungsten carbide bushing processing equipment is evolving towards several cutting-edge directions.
Emphasis on Both High Precision and High Efficiency: Future processing equipment will prioritize both processing accuracy and efficiency. By adopting advanced processing technologies and processes, it will achieve mass production of high-quality and high-efficiency products, meeting the market’s urgent demand for superior products.
Intelligent and Automated Upgrades: Leveraging advanced sensors, control systems, and artificial intelligence technologies, processing equipment will undergo intelligent and automated upgrades. This will reduce manual intervention, enhance production efficiency and product quality, and make the processing more intelligent and efficient.
Green, Environmentally Friendly, and Energy-Saving Designs: With the growing awareness of environmental protection, future processing equipment will place greater emphasis on green, environmentally friendly, and energy-saving designs. By utilizing eco-friendly materials and optimizing energy utilization, it will reduce energy consumption and waste emissions, achieving sustainable development.
Modular and Flexible Designs: To accommodate the processing needs of tungsten carbide bushings with different specifications and sizes, processing equipment will adopt modular and flexible design concepts. Users can flexibly configure and adjust the equipment according to their actual needs, improving equipment utilization and adaptability.
V. Conclusion: Envisioning a Bright Future for Processing Equipment
Tungsten carbide bushing processing equipment, as a crucial piece of equipment in modern mechanical manufacturing, directly impacts the production efficiency and service life of related products. Through continuous optimization of design, enhancement of processing accuracy and efficiency, and realization of intelligent and automated upgrades, we have every reason to believe that future tungsten carbide bushing processing equipment will play an even more vital role in driving industrial development, injecting new vitality into the prosperity of the manufacturing industry.
Publicações relacionadas
- New Chapter in Tungsten Carbide Precision Components Manufacturing: Unlocking the Secrets to Superior Performance
- The Critical Role of Tungsten Carbide in Precision Industries
- Guide to Tungsten Carbide Punches
- Trefilagem de perfis Polimento de matrizes: da precisão à nanoescala ao fabrico ecológico inteligente