Guide to Tungsten Carbide Punches
In the realm of precision manufacturing, tungsten carbide punches stand as the “needles of industrial sewing machines,” delivering 0.01mm-level dimensional accuracy that underpins the fabrication of automotive engine covers, 5G […]
In the realm of precision manufacturing, tungsten carbide punches stand as the “needles of industrial sewing machines,” delivering 0.01mm-level dimensional accuracy that underpins the fabrication of automotive engine covers, 5G base station heat sinks, and even surgical instrument markings. This article dissects the seven-dimensional classification system and battle-tested application strategies of tungsten carbide punches, empowering readers to seize technological leadership in precision stamping.
1. Form Follows Function: The 3D Warfare of Shape-Based Classification
1.1 Spherical Punches – The “Tai Chi Masters” of Curved Stamping
当社の工場事業:超硬部品、金型部品、医療用射出成形金型、精密射出成形金型、テフロンPFA射出成形、PFAチューブ継手。電子メール:[email protected],whatsapp:+8613302615729。
- Structural Secrets: R0.5-3mm spherical head design with 30°-45° taper transitions
- Scenario Code: Excelling in 0.5-2mm stainless steel blind hole stamping, achieving >800,000 strokes in Tesla’s battery tray vent valve production
- Avoidance Tactics: Switch to dual-curvature compound punches when stamping depth exceeds 3x ball diameter
1.2 Flat Punches – The “Swift Swordsmen” of Linear Cutting
- Technical Benchmarks: ≤0.003mm edge straightness, Ra0.2μm surface roughness
- Noise Reduction Innovation: 45°×0.1mm chamfering reduces stamping noise by 12dB (1/3 sound pressure of conventional punches)
- Iconic Application: Scratch-free pre-punching for MacBook metal casings with vacuum suction systems
1.3 Specialty Punch Matrix – The “Transformers” of Customized Demands
- Hexagonal Pins: Conquering M3-M12 thread bottom hole cold forging, boosting thread qualification rates from 78% to 99.2% in Tesla drive motor housing production
- Elliptical Pins: Breaking the 0.8mm×1.5mm ultra-narrow ellipse hole limit for Huawei Mate series antenna windows
- Forming Pins: Integrating multi-stage steps for “one-shot forming + deburring” in aerospace fastener cold heading
2. Specialized Warfare: Precision Strikes in Application-Based Classification
2.1 Precision Trifecta: SKD/SKH/ASP Showdown
素材 | Hardness (HRC) | Impact Toughness (J/cm²) | Typical Scenarios |
---|---|---|---|
SKD11 | 60-62 | 15-20 | 0.1mm-level LED bracket precision punching |
SKH51 | 64-66 | 10-15 | Automotive airbag housing progressive dies |
ASP23 | 68-70 | 25-30 | Medical titanium alloy implant micro-hole machining |
2.2 Process Special Forces: Invisible Champions in Niche Scenarios
- Pilot Pins: Laser-positioned systems achieve ±0.01mm hole placement in 0.3mm copper foil FPC stamping
- Sub-mother Pins: Modular designs enable “punching + flanging + riveting” tri-station synchronization in laptop hinge components
- Drawing Pins: 2.5D curved drawing breakthrough for 0.3mm-wall tear-free side button holes in smartwatch cases
- Sensor Pins: Integrated pressure sensors and displacement encoders enable 0.001mm process monitoring in semiconductor leadframe stamping
3. Material Dilemmas: The Art of Balancing Performance and Cost
3.1 Tungsten Carbide vs. High-Speed Steel: Quantified Performance Showdown
メートル | Tungsten Carbide (YG15) | High-Speed Steel (SKH51) | Critical Application Scenarios |
---|---|---|---|
Hardness (HRC) | 89-91 | 64-66 | ≥2mm 304 stainless steel stamping |
Wear Life | 15× | 1× | Air conditioner compressor scroll die |
Chipping Resistance | ★★★★☆ | ★★★☆☆ | Gearbox housing irregular hole machining |
Cost Factor | 3.2 | 1.0 | Annual production >500,000 molds |
3.2 Composite Material Revolution: Nanocrystalline Coating Technology
- TiAlN nanocrystalline coatings extend punch life by 300% when machining hardened steel
- An EV battery manufacturer reduced annual mold maintenance costs from ¥280,000 to ¥67,000 through this technology
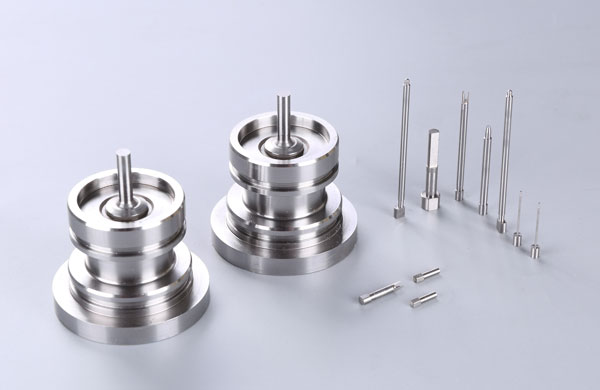
4. Special Operations: Breakthrough Weapons for Extreme Conditions
4.1 Cemented Carbide Punch Rods – Nemeses of Ultra-Hard Materials
- WC-10%Co ultrafine-grained substrates maintain 0.005mm dimensional stability when processing HRC62 tool steel
- An aerospace enterprise boosted satellite solar panel substrate punching efficiency by 400% using this technology
4.2 3D-Printed Specialty Pins – The “Magic” of Topology Optimization
- SLM-fabricated internal honeycomb structures reduce weight by 40% while maintaining strength
- A medical device company customized titanium alloy specialty pins to achieve 99.8% yield in cardiac stent laser cutting positioning holes
5. Battlefield Tactics: The 3D Defense System for Punch Management
5.1 “Three-Pronged Approach” for Fitment Testing
- Optical projector contour measurement (0.001mm accuracy)
- Hardness tester HV value spot checks (±2% fluctuation tolerance)
- Dynamic simulation testing (100,000-stroke continuous punching validation)
5.2 Intelligent Early Warning Systems
- Acoustic emission sensors with AI algorithms detect punch crack initiation signals
- A home appliance manufacturer reduced sudden mold failures by 76% using this system
5.3 Lubrication Revolution: Nano Self-Repairing Coatings
- MoS₂-WS₂ composite coatings enable “dry friction → self-lubrication” state switching
- A 3C precision mold factory reduced punching force by 18% and mold temperature rise by 12°C through this technology
6. Future Battlefields: The Bugle Call of New Productivity Forces
6.1 Technology Convergence Trends
- Digital twin technology: Predictive maintenance cycles shortened by 60% through punch wear simulation models
- Ultrafast laser processing: 0.005mm-level microstructure machining on punch edges, breaking traditional EDM limits
6.2 Industrial Upgrade Roadmap
- Automotive: Expanding into 7000-series aluminum, magnesium alloy lightweight material stamping
- Electronics: Adapting to 0.03mm ultra-thin glass, PI film flexible material processing
- Military: Breakthroughs in titanium alloy, superalloy difficult-to-machine material stamping
7. Ultimate Insight: The Paradigm Shift from Tools to Systems
Tungsten carbide punches have evolved from standalone tools into intelligent “material-structure-process” systems. A leading enterprise achieved:
- Design Phase: CAE simulation-optimized punch geometric parameters
- Production Phase: IoT-based real-time punch condition monitoring
- Maintenance Phase: AR-guided remote replacement operations
Resulting in 42% lower mold costs and 35% shorter delivery cycles
結論
In the Industry 4.0 era, tungsten carbide punches are undergoing a paradigm shift from “experience-driven” to “data-driven” operations. Mastering their classification logic and application strategies is no longer just a technical necessity but a key to unlocking corporate competitive advantages. When 0.01mm precision differences determine million-dollar orders, are you prepared for this “millimeter-level warfare” of precision manufacturing?