Tungsten Carbide Usage Guide
Tungsten carbide, also known as hard alloy, is an alloy material formed by pressing and sintering metal powders such as tungsten and cobalt. Thanks to its high hardness, excellent wear […]
Tungsten carbide, also known as hard alloy, is an alloy material formed by pressing and sintering metal powders such as tungsten and cobalt. Thanks to its high hardness, excellent wear resistance, and high-temperature resistance, tungsten carbide finds wide applications in various fields including mechanical processing, mold manufacturing, and oil drilling, becoming an indispensable “right-hand man” in industrial production. However, to fully leverage the advantages of tungsten carbide, ensure its proper use, and extend its service life, there are numerous crucial considerations during its usage. Next, this article will elaborate on the precautions for using tungsten carbide from four aspects: purchase, processing, usage, and safety.
I. Careful Selection: Strictly Control Quality and Specifications
Quality First: Opt for Products from Reputable Manufacturers
When purchasing tungsten carbide materials, it is essential to choose products from regular manufacturers. Regular manufacturers have strict production processes and quality control systems, which can ensure the reliable quality of tungsten carbide. High-quality tungsten carbide materials feature a uniform microstructure, high hardness, and excellent wear resistance. Avoid buying products with unknown sources or unreliable quality; otherwise, material quality issues may lead to failures during use, causing production interruptions and unnecessary losses.
当社の工場事業:超硬部品、金型部品、医療用射出成形金型、精密射出成形金型、テフロンPFA射出成形、PFAチューブ継手。電子メール:[email protected],whatsapp:+8613302615729。
Specifications Matching: Select According to Actual Needs
Different application scenarios and working conditions have varying requirements for the specifications of tungsten carbide. Therefore, when purchasing, it is crucial to fully consider actual needs and accurately select the appropriate specifications. For example, in precision mold manufacturing, tungsten carbide materials with high dimensional accuracy and good surface finish are required; while in oil drilling, tungsten carbide with higher strength and toughness is preferred. Only when the selected materials perfectly match the working conditions can they deliver optimal performance.
II. Precision Processing: Grasp Key Process Points
Tool Adaptation: Tackle High-Hardness Challenges
Due to the extremely high hardness of tungsten carbide, ordinary tools often struggle to cut it during processing. Therefore, it is necessary to use tools with higher hardness. At the same time, the sharpness of the tools is also of great importance. Dull tools not only significantly reduce processing efficiency but may also damage the tungsten carbide material during cutting, affecting processing quality. Therefore, regularly check the sharpness of the tools and promptly replace worn ones.
Parameter Optimization: Ensure Processing Stability
During tungsten carbide processing, the setting of cutting parameters directly affects the processing effect and tool life. Parameters such as cutting speed, feed rate, and cutting depth need to be reasonably coordinated. Excessive cutting speed or feed rate can accelerate tool wear and even lead to tool breakage, posing serious safety hazards to production. Therefore, precisely adjust the cutting parameters according to the actual situation, including the material properties of tungsten carbide, tool performance, and processing requirements, to ensure a stable, safe, and efficient processing process.
Cooling and Lubrication: Enhance Processing Quality
Using cutting fluid for cooling and lubrication during the processing is an indispensable step. Cutting fluid can effectively reduce the cutting temperature, minimizing tool wear caused by high temperatures and extending tool service life. Meanwhile, it also serves as a lubricant, reducing friction resistance during cutting and improving processing accuracy and surface quality. Therefore, ensure that the cutting fluid is sufficient and evenly sprayed on the processing area to fully exert its cooling and lubricating effects.
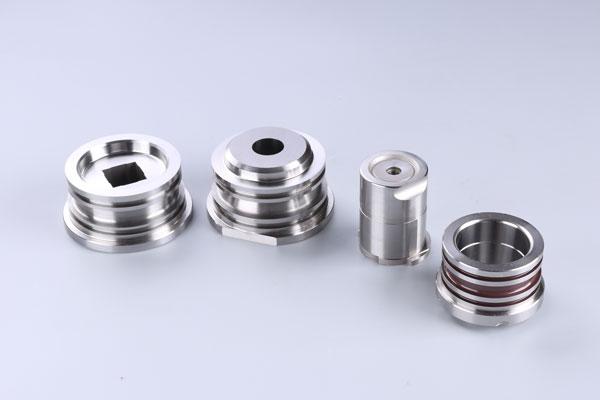
III. Proper Usage: Emphasize Daily Maintenance
Avoid Impact: Protect Brittle Materials
Although tungsten carbide has high hardness, it is also relatively brittle. During use, strong impacts and vibrations should be avoided to prevent the tungsten carbide material from cracking or breaking. Especially during high-load operations, effective vibration reduction measures should be taken to create a safe and stable working environment for the tungsten carbide material and ensure its normal operation.
Keep Clean and Dry: Prevent Corrosion and Rust
Tungsten carbide materials should be stored in a dry and clean environment, away from moisture and corrosive substances. A humid environment can easily cause tungsten carbide to rust or corrode, reducing its performance and service life. Therefore, regularly inspect and clean the storage environment to maintain dryness and ventilation. Additionally, promptly clean dirt and impurities on the surface of tungsten carbide during use to prevent them from causing damage to the material.
Regular Inspection and Maintenance: Address Anomalies Promptly
Establish a regular inspection and maintenance system during use. Conduct comprehensive inspections on tungsten carbide materials regularly. If anomalies such as surface cracks or wear are found, handle or replace them on time. For minor cracks, welding methods can be used for repair; for severely worn parts, new ones should be replaced promptly to ensure that the tungsten carbide materials are always in good working condition.
IV. Safety First: Implement Protection and Operation Norms
Personal Protection: Safeguard Physical Well-being
When operating tungsten carbide materials, personal protective measures are essential. Operators should wear protective equipment such as work clothes, gloves, and goggles to prevent injuries from flying debris or burns during operation. At the same time, ensure that the working environment meets safety and hygiene standards, such as maintaining good ventilation and sufficient lighting, to create a safe and comfortable working environment for operators.
Standardized Operation: Eliminate Rule-breaking Behaviors
When using tungsten carbide for work, strictly abide by the operation procedures and safety regulations. Prohibit rule-breaking operations or overloading of tungsten carbide materials to avoid safety accidents. For example, during processing, do not arbitrarily change processing parameters or operation sequences; when handling tungsten carbide materials, use appropriate tools and methods to prevent the materials from falling and causing injuries. In case of emergencies, immediately stop the operation and seek help from professionals promptly.
Proper Disposal: Avoid Environmental Pollution
Waste tungsten carbide materials contain certain heavy metal components. If disposed of randomly or incinerated, they can cause severe environmental pollution and harm human health. Therefore, dispose of waste tungsten carbide materials by relevant regulations. Hand them over to professional recycling institutions for recycling and reuse, achieving resource recycling and reducing negative impacts on the environment.
In conclusion, the use of tungsten carbide is a systematic project that requires strict control in all aspects, including purchase, processing, usage, and safety. Only by strictly adhering to relevant regulations and operation procedures can we ensure the proper use of tungsten carbide, extend its service life, and safeguard the safety and health of operators, providing strong support for the efficient and stable operation of industrial production.