How to use tungsten carbide to process efficiency and extend tool life
In the vast realm of mechanical processing, tungsten carbide, also known as cemented carbide, shines brightly like a dazzling star. It is meticulously crafted through powder metallurgy by combining hard […]
In the vast realm of mechanical processing, tungsten carbide, also known as cemented carbide, shines brightly like a dazzling star. It is meticulously crafted through powder metallurgy by combining hard compounds of refractory metals with binding metals. This unique alloy boasts a host of excellent properties, including high hardness, wear resistance, good strength and toughness, heat resistance, and corrosion resistance. Whether it’s turning, milling, planing, or drilling, tungsten carbide plays a pivotal role in various mechanical processing fields, making significant contributions to improving processing efficiency and ensuring processing quality. However, just like a high-performance machine, this “processing expert” has its own set of “operating rules.” Only by following a series of usage precautions can we fully unleash its potential and extend its service life. Next, let’s delve into the mysteries of using tungsten carbide.
I. Careful Selection and Rational Use
When choosing tungsten carbide cutting tools, it’s akin to selecting the right weapon for a crucial battle. We must take into account multiple factors comprehensively, such as specific processing requirements, material hardness, and the working environment. Different grades of tungsten carbide are like soldiers with distinct personalities, each having its own unique properties and applicable scope. Only by picking the most suitable “soldier” can we ensure both high processing quality and efficiency.
Onze fabriek business: carbide onderdelen, schimmel onderdelen, medische spuitgietmatrijzen, precisie spuitgietmatrijzen, teflon PFA spuitgieten, PFA buismontage. e-mail: [email protected],whatsapp:+8613302615729.
During the use of these tools, strict adherence to operating procedures is essential, just as a general must command the troops with precision. Avoid using the cutting tools under conditions that exceed their design capabilities. Excessive cutting speeds, large feed rates, or deep cutting depths can all be the “straw that breaks the camel’s back,” leading to premature tool failure.
II. Cleanliness and Dryness: A Vital Care Routine
Tungsten carbide cutting tools need to maintain cleanliness and dryness during their “combat” operations. The chips and oil stains generated during the cutting process are like hidden enemies that can significantly affect the cutting effect and tool life. Therefore, it’s crucial to promptly remove these “enemies” to keep the tools in top-notch condition.
Moreover, the storage environment of the tools is of utmost importance. They should be placed in a dry and well-ventilated “base camp” to shield them from the harmful effects of moisture and corrosive gases, just as soldiers need a safe and comfortable rest area before their next mission.
III. Avoiding Collisions and Vibrations: A Delicate Balance
Although tungsten carbide cutting tools are extremely hard, they are also relatively brittle, similar to a sharp yet fragile sword. Extra caution is required during use to prevent collisions with other hard objects or exposure to severe vibrations. These external forces act like ruthless “assassins,” potentially causing cracks or chipping in the tools, severely undermining their service life and cutting performance. Hence, we must treat each tool with the utmost care, as if it were a precious treasure.
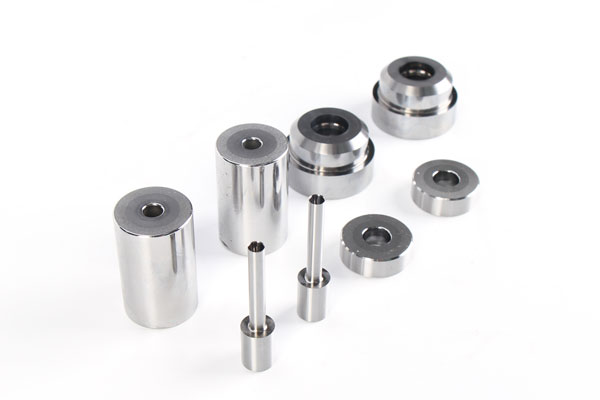
IV. Regular Inspection and Maintenance: A Proactive Approach
To ensure that tungsten carbide cutting tools are always ready for action, regular inspection and maintenance are indispensable. This is like conducting regular physical examinations for soldiers to detect and address potential issues promptly. The inspection should cover aspects such as tool wear, chipping, and cracks. Once these problems are identified, immediate actions such as regrinding or replacement should be taken to restore the tools’ combat effectiveness. Additionally, regular cleaning and lubrication of the tools are necessary, just as maintaining soldiers’ weapons to keep them in optimal working condition.
V. Skillful Use of Cutting Fluid: Enhancing Efficiency and Reducing Wear
During the cutting process, cutting fluid serves as a silent “support troop,” effectively reducing the cutting temperature, minimizing tool wear, and improving processing quality and efficiency. However, using cutting fluid requires certain skills. Firstly, select the appropriate type of cutting fluid to ensure compatibility with tungsten carbide materials, just as choosing the right supplies for soldiers to maximize their effectiveness. Secondly, control the flow rate and pressure of the cutting fluid to avoid causing shock or damage to the tools, similar to regulating the supply of resources to prevent wastage. Finally, replace the cutting fluid regularly to maintain its cleanliness and effectiveness, ensuring that the “support troop” is always in top form.
VI. Safety Precautions: Putting Life First
When using tungsten carbide cutting tools, flying chips and high temperatures can pose potential threats to operators, just as flying shrapnel and intense heat on the battlefield endanger soldiers. Therefore, operators must take comprehensive safety precautions, such as wearing protective goggles and gloves, to shield themselves from harm, just as soldiers put on sturdy armor. At the same time, strict compliance with safety operating procedures is essential to prevent accidents and ensure that every processing operation is carried out in a safe environment.
VII. Training and Education: Elevating Skills and Awareness
To enhance operators’ skills in using tungsten carbide cutting tools and raise their safety awareness, enterprises should conduct regular training and education programs. This is like providing systematic military training for soldiers, covering basic knowledge of tungsten carbide materials, tool selection and use, and safety operating procedures. Through training and education, operators’ professional levels can be improved, reducing tool damage and safety accidents caused by misoperations, and turning every operator into a “master” in handling tungsten carbide cutting tools.
In conclusion, using tungsten carbide involves a wide range of considerations, from careful selection and rational use to maintaining cleanliness and dryness, avoiding collisions and vibrations, conducting regular inspection and maintenance, skillfully using cutting fluid, taking safety precautions, to strengthening training and education. Only by fully considering and strictly following these precautions can we enable tungsten carbide cutting tools to shine even brighter in the field of mechanical processing, creating greater value for enterprises.