Profile Wire Drawing Die Polishing: From Nanoscale Precision to Green Smart Manufacturing
In high-end manufacturing sectors such as new energy vehicle wiring harnesses, 5G communication optical fibers, and aerospace superconducting materials, profile wire drawing dies serve as “metal sculptors.” Their intricate internal […]
In high-end manufacturing sectors such as new energy vehicle wiring harnesses, 5G communication optical fibers, and aerospace superconducting materials, profile wire drawing dies serve as “metal sculptors.” Their intricate internal structures—including helical holes, irregular tapered channels, and micron-level flow paths—directly dictate the surface quality and mechanical properties of metal wires. However, the polishing process for such dies has long been mired in the dilemma of “precision vs. efficiency.” This article dissects the evolution of profile wire drawing die polishing technology, from traditional craftsmanship to intelligent fluidics, revealing the transformative密码 (lit. “code,” metaphorically “key drivers”) of this “invisible battlefield” in industrial innovation.
I. The Dual Role of Profile Wire Drawing Die Polishing: Aesthetic Enhancement and Lifespan Extension for Metal Wires
1. Surface Quality Revolution
Наш завод занимается: твердосплавные детали, детали пресс-форм, медицинские пресс-формы для литья под давлением, прецизионные пресс-формы для литья под давлением, литье тефлона PFA, фитинги для труб PFA. e-mail: [email protected],whatsapp:+8613302615729.
- Friction Reduction & Efficiency Gains: Ultra-precision polished die interiors reduce copper wire drawing resistance by 40%, lowering surface roughness (Ra) from 1.6μm to below 0.05μm—meeting mirror-finish requirements for semiconductor lead frame wires.
- Performance Leap: Polishing quality directly impacts wire tensile strength (15–20% improvement) and fatigue life (3x extension), becoming a core competitive edge in premium wire manufacturing.
2. Cost-Benefit Analysis
- High-quality polishing extends die lifespan from 30,000 to 150,000 drawing cycles, slashing per-cycle wire processing costs by 67%.
- Деловое исследование: An automotive wiring harness manufacturer reduced die repair rates from 28% to 3% after adopting fluidic polishing, saving over ¥2 million annually in die costs.
II. The Triad of Polishing Technologies: From “Artisanal Craft” to “Fluidic Revolution”
(A) Traditional Polishing: Trapped in the “Human Efficiency Paradox”
- Process Pains:
- Reliance on “master craftsmen” experience limits manual grinding efficiency to 0.2m²/h with ±20% consistency errors;
- Polishing coverage in irregular die blind spots drops below 60%, fostering stress concentration points.
- **Industry Toll*: A precision electronic connector firm suffered a 12% wire fracture rate due to inconsistent polishing, incurring annual losses exceeding ¥10 million.
(B) Fluidic Polishing: The “Micro-Sculptor” for Irregular Holes
1. Technical Principles
- Couples polymer silicon carbide/nano-diamond abrasives (particle size adjustable from 0.5–50μm) with high-pressure fluids for “flexible cutting + micro-rolling” composite action.
- Benchmarking:MetricFluidic PolishingManual PolishingSurface RoughnessRa≤0.05μmRa≥0.2μmProcessing Speed5–8m²/h0.2m²/hHole Profile Retention≥98%≤75%
2. Industry Breakthrough Cases
- Cemented Carbide Dies: For aerospace engine superalloy wire dies, initial Ra0.8μm→post-polish Ra0.12μm, quintupling lifespan;
- Ceramic Micro-Hole Dies: Achieved damage-free polishing of Φ0.1mm intersecting holes in fuel cell proton exchange membrane dies, attaining 90%+ mirror finish on hole walls.
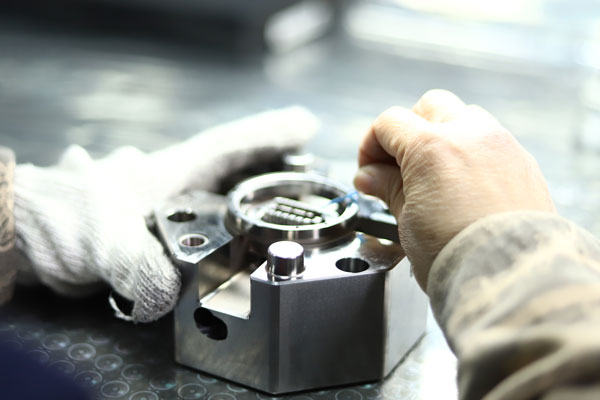
III. Fluidic Polishing: The “Universal Key” for Profile Dies
1. Material Versatility
- Metal Matrix: Covers soft metals (HRC20–30, e.g., copper-aluminum) to hardened steels (HRC60+), carbides (HRC85+), enabling nanoscale polishing;
- Cross-Industry Applications:
- Semiconductor Ceramics: Polished SiC spinnerets, reducing surface defect density from 120/cm² to 3/cm²;
- Composites: Resolved fiber delamination in carbon fiber-reinforced resin dies during traditional polishing.
2. Process Penetration
- EDM/Laser Post-Treatment: Removes hardened layers (up to 50μm deep) from processing, restoring material’s original fatigue strength;
- Microstructure Preservation: Maintains functional structures like micro-grooves/holes during polishing (tolerance ≤1μm).
IV. Technological Evolution: The “Intelligent Transformation” and “Green Shift” of Polishing
(A) Automation & Intelligence: From “Machine Substitution” to “Machine Cognition”
- AI Vision Inspection: Robotic polishers with industrial cameras detect 0.01mm-level die defects in real time, autonomously planning polishing paths;
- Digital Twin Systems: CAE-simulated polishing processes predict die deformation, cutting trial-and-error costs by 80%;
- Деловое исследование: A 5G filter manufacturer achieved 98% yield (up from 65%) and 60% shorter lead times after adopting intelligent polishing lines.
(B) High Precision & Ultra-Efficiency: Nanoscale Precision at “Lightning Speed”
- Magnetorheological Polishing: Magnetic field-controlled abrasive distribution achieves Ra0.01μm-level polishing for aerospace titanium alloy wire dies;
- Ultrasonic-Assisted Fluidic Polishing: 20kHz ultrasonic vibrations triple polishing efficiency, ideal for large dies (e.g., Φ200mm wire drawing wheels).
(C) Green Manufacturing: From “End-of-Pipe Treatment” to “Source Carbon Reduction”
- Eco-Abrasives: Water-based nano-alumina abrasives replace oil-based counterparts, slashing VOC emissions by 90%;
- Resource Recycling: Centrifugal separation recovers 95% of abrasives from polishing waste, with water recycling rates exceeding 80%;
- Policy Drivers: Under EU “Carbon Border Tax,” enterprises adopting green polishing reduce export costs by 12–15%.
Conclusion: Polishing Technology—The “Invisible Driver” of High-End Manufacturing
In the manufacturing jungle where “precision determines survival,” profile wire drawing die polishing is emerging from the shadows. With deep integration of AI, new materials, and green processes, this field will spawn more “disruptive innovations”: Perhaps soon, a “thinking” polishing robot could streamline complex die polishing as effortlessly as brewing coffee.