Eingehende Analyse der Ursachen für die Verformung von Wolframkarbidprodukten
EinleitungWolframkarbid ist für seine außergewöhnliche Härte, Verschleißfestigkeit und hervorragende Bearbeitbarkeit bekannt und nimmt in Branchen wie dem Formenbau, dem Präzisionswerkzeugbau und der Luft- und Raumfahrt eine Schlüsselposition ein. Während der Produktion und [...]
Einführung
Wolframkarbid ist für seine außergewöhnliche Härte, Verschleißfestigkeit und hervorragende Bearbeitbarkeit bekannt und nimmt in Branchen wie dem Formenbau, dem Präzisionswerkzeugbau und der Luft- und Raumfahrt eine Schlüsselposition ein. Während der Produktion und Anwendung weisen Hartmetallprodukte jedoch häufig Verformungsprobleme wie Biegen oder Verziehen auf, die sich direkt auf die Bearbeitungsgenauigkeit und die Lebensdauer auswirken. In diesem Artikel werden die Ursachen für die Verformung von Wolframkarbid aus verschiedenen Blickwinkeln beleuchtet, darunter Materialwissenschaft, Prozessparameter und Umweltkontrollen, unterstützt durch experimentelle Daten und Fallstudien, um die Ursachen systematisch zu analysieren und gezielte Lösungen vorzuschlagen.
I. Ungleichgewicht des Kohlenstoffgradienten: Der unsichtbare Faktor im Sinterprozess
Während der Entparaffinierungs-, Vorsinterungs- und Sinterphasen entstehen durch dynamische Veränderungen des Kohlenstoffgehalts im Wolframkarbid Kohlenstoffgradienten. Wenn die Konzentration von CXHY-Verbindungen in H₂-Sinteratmosphären Grenzwerte überschreitet oder der Kohlenstoffgehalt des Rohmaterials schlecht kontrolliert wird, sind großformatige und längliche/flache Produkte besonders anfällig. So wies beispielsweise eine von einem bestimmten Unternehmen hergestellte Φ150mm-Wolframkarbidscheibe eine wellenförmige Verformung von 0,3mm auf, die auf eine 12% schnellere Entkohlung an den Rändern im Vergleich zur Mitte zurückzuführen war. Diese ungleichmäßige Kohlenstoffverteilung verändert die lokalen Spannungsfelder der Phasenumwandlung und ist ein wichtiger Auslöser der Verformung.
Unser Fabrikgeschäft: Hartmetallteile, Formteile, medizinische Spritzgussformen, Präzisionsspritzgussformen, Teflon-PFA-Spritzguss, PFA-Rohrverschraubungen. E-Mail: [email protected],whatsapp:+8613302615729.
II. Kobalt-Phasenwanderungseffekt: Mikroskopische Verformung unter dem Einfluss der Benetzbarkeit
Während des Vakuumsinterns führen Benetzbarkeitsunterschiede zwischen der Kobaltphase und den Graphittiegeln zu einer gerichteten Migration. Eine schlechte Kobaltbenetzbarkeit führt zu einer Kobaltanreicherung auf der Oberseite, was bei einer Charge von Hartmetallschaufeln zu einer konvexen Verformung von 0,15 mm führt. Umgekehrt führt eine übermäßige Benetzbarkeit zu einer Kobaltinfiltration nach unten, was zu konkaven Oberflächenmerkmalen führt. Experimentelle Daten zeigen, dass ein Anstieg des Kobaltverteilungsgradienten um 5% die Planitätsabweichung um 0,08 mm vergrößert. Diese mikroskopisch kleine ungleichmäßige Schrumpfung beeinträchtigt direkt die geometrische Präzision.
III. Heterogenität des Temperaturfeldes: Gradienten-induzierte Katastrophen durch Wärmeleitung
Temperaturgradienten während des Sinterns wirken sich synergetisch auf die Kobaltmigration aus. Eine Präzisionsform, die mit einem Temperaturunterschied von 80℃ zwischen den Rändern und der Mitte gesintert wurde, wies einen Unterschied im Kobaltgehalt von 12% auf, was zu einer konischen Verformung von 0,2 mm führte. Temperaturgradienten verschlimmern nicht nur die Inhomogenität der Kobaltphase, sondern führen auch über thermische Spannungen zu Mikrorissen, die in einem Bauteil für die Luft- und Raumfahrt aufgrund der Spannungskonzentration zu Sprödbrüchen führen. Die Wärmebildanalyse zeigt, dass ±15℃ Temperaturschwankungen lokale Verformungen von 0,05 mm auslösen können.
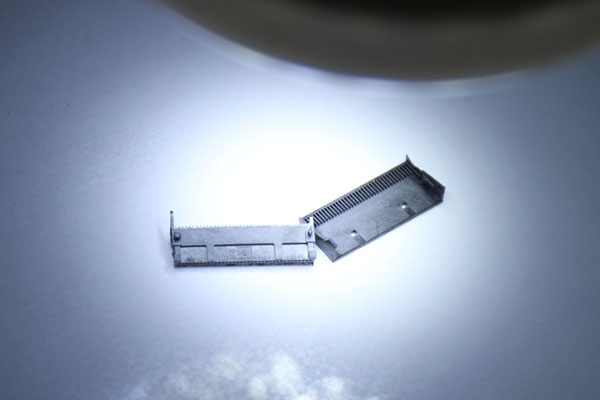
IV. Kumulativer Effekt des Dichtegradienten: Inhärente Mängel bei Verdichtungsprozessen
Durch Kraftabschwächung und ungleichmäßige Materialbelastung während der Verdichtung entstehen Dichtegradienten. Eine komplexe Hohlraumform, die mit 12% verdichtet wurde, wies in den Ecken eine geringere Dichte auf als in den flachen Bereichen und wies eine um 0,4 mm unterschiedliche Sinterschwindung auf, was zu Maßabweichungen im Hohlraum führte. Dichtegradienten verändern die anisotrope Schwindung, was zu einer asymmetrischen Produktverformung führt. Die Röntgentomographie zeigt, dass Dichtefluktuationen von ±5% zu geometrischen Abweichungen von 0,1 mm führen können.
V. Synergistische Kopplung umfassender Faktoren: Kollaborative Deformationsmechanismen
Neben den Kernfaktoren spielen auch Belastungsmethoden, Variationen des Schrumpfungskoeffizienten und Umweltbelastungen eine Rolle. Ein Unternehmen erlebte 0,1 mm Parallelitätsabweichungen bei Produkten aufgrund von Druckspannungen zwischen den Produkten, die durch eine zu hohe Ladedichte verursacht wurden. Feuchtigkeitsschwankungen verringerten die Maßhaltigkeit von 30% in einer Charge von Schneidwerkzeugen. Diese Faktoren verändern die konstitutiven Beziehungen zwischen den Werkstoffen und bilden komplexe Kopplungen mit den Kernmechanismen - Experimente zeigen, dass die Wechselwirkungen mehrerer Faktoren die Verformungsgrößen verdreifachen können.
VI. Systematische Präventionsstrategien: Qualitätskontrollsysteme für die gesamte Kette
- Optimierung des Materialdesigns: Implementierung von Designs mit abgestuftem Kohlenstoffgehalt. Das zweiphasige Wolframkarbidmaterial eines Unternehmens mit einer Kohlenstoffgradientensteuerung von ±0,03% reduzierte die Verformungsraten um 60%.
- Prozessparameter Präzisionskontrolle: Einsatz einer synergetischen Temperatur-Druck-Regelung. Die PID-Regelung während des Sinterns von Präzisionsteilen reduzierte die Temperaturschwankungen auf ±5℃ und verbesserte die Planarität auf 0,02 mm.
- Upgrades der Ausrüstung: Einführung isostatischer Presssysteme, die eine gleichmäßige Dichte von 98% erreichen und die Verformung der Form auf 0,05 mm begrenzen.
- Systeme zur Rückverfolgbarkeit von Qualität: Einrichtung einer durchgängigen Datenüberwachung von den Rohstoffen bis zum Endprodukt. SPC-Analyse senkte die Fehlerquote in einem Unternehmen von 15% auf 2,3%.
Schlussfolgerung
Die Verformung von Hartmetallprodukten resultiert aus dem Zusammenspiel von Materialeigenschaften, Prozessparametern und Umgebungsbedingungen. Durch den Aufbau eines Vier-in-Eins-Präventionssystems, das "Materialdesign - Prozessoptimierung - Anlagensicherung - Qualitätskontrolle" umfasst, gelang es einem Unternehmen, die kritische Produktverformung auf 0,05 mm zu begrenzen und die Produktqualifikationsrate auf 99,2% zu steigern. Mit zukünftigen Anwendungen intelligenter Sensor- und digitaler Zwillingstechnologien wird die Kontrolle der Verformung von Hartmetall in Richtung Submikrometerpräzision voranschreiten und die technologische Innovation in der High-End-Fertigung weiter vorantreiben.