Entschlüsselung der Geheimnisse des Hartmetallschleifens
In der weiten Landschaft der industriellen Produktion ragt Wolframkarbid, auch bekannt als Hartmetall, wie ein leuchtender Stern hervor. Mit seiner außergewöhnlichen Härte, seiner bemerkenswerten Verschleißfestigkeit und seiner hervorragenden Hochtemperaturleistung [...]
In der weiten Landschaft der industriellen Produktion ragt Wolframkarbid, auch bekannt als Hartmetall, wie ein leuchtender Stern hervor. Mit seiner außergewöhnlichen Härte, seiner bemerkenswerten Verschleißfestigkeit und seiner hervorragenden Hochtemperaturleistung spielt es eine unverzichtbare Rolle in verschiedenen Branchen. Ob bei Zerspanungswerkzeugen, im Formenbau oder bei der Herstellung hochwertiger Komponenten für die Luft- und Raumfahrt und die Automobilindustrie, Wolframkarbid ist unersetzlich.
Doch jede Medaille hat zwei Seiten. Die sehr hohe Härte von Wolframkarbid verleiht ihm zwar seine hervorragenden Eigenschaften, erhöht aber auch die Schwierigkeit der Bearbeitung, insbesondere beim Schleifen, erheblich. Heute wollen wir uns eingehend mit der Schleiftechnologie von Hartmetallprodukten befassen und ihre einzigartigen Merkmale, Prozessabläufe, häufige Probleme und entsprechende Lösungen enträtseln, mit dem Ziel, wertvolle Erkenntnisse für Praktiker in verwandten Bereichen zu liefern.
Unser Fabrikgeschäft: Hartmetallteile, Formteile, medizinische Spritzgussformen, Präzisionsspritzgussformen, Teflon-PFA-Spritzguss, PFA-Rohrverschraubungen. E-Mail: [email protected],whatsapp:+8613302615729.
I. Besondere Herausforderungen beim Schleifen von Wolframkarbid
Das Schleifen von Wolframkarbid ist mit einer Reihe von Herausforderungen verbunden, die die Fähigkeiten und das Fachwissen des Bearbeiters auf eine harte Probe stellen.
1. Unvergleichliche Härte
Die Härte von Wolframkarbid übertrifft die von gewöhnlichem Stahl bei weitem und steht damit an der Spitze der Härtehierarchie. Diese Eigenschaft macht die Auswahl und Verwendung von Schleifscheiben im Schleifprozess zu einem entscheidenden Faktor. Gewöhnliche Schleifscheiben sind wie Eierschalen, die an einem Felsen zerschellen, wenn sie mit Wolframkarbid konfrontiert werden. Sie nutzen sich schnell ab und beeinträchtigen sowohl die Bearbeitungsgenauigkeit als auch die Effizienz.
2. Abriebfeste "Rüstung"
Die bemerkenswerte Verschleißfestigkeit von Wolframkarbid ist ein zweischneidiges Schwert. Sie ermöglicht es dem Material, rauen Bedingungen zu widerstehen, stellt aber auch ein Problem beim Schleifen dar. Die geringe Abtragsleistung erfordert mehr Zeit und Mühe, und die Anforderungen an die Bearbeitungsgenauigkeit sind noch höher. Ein kleiner Fehltritt kann dazu führen, dass alle bisherigen Bemühungen umsonst waren.
3. Wärmeleitfähigkeit "Mangel"
Wolframkarbid hat eine niedrige Wärmeleitfähigkeit, so als ob man dem Werkstück einen "Isoliermantel" anziehen würde. Die beim Schleifen entstehende Wärme kann nur schwer abgeführt werden, wodurch die Oberflächentemperatur des Werkstücks schnell ansteigt. Dies beeinträchtigt nicht nur die Bearbeitungsqualität und führt zu Oberflächenfehlern, sondern verkürzt auch die Lebensdauer der Schleifscheibe und erhöht die Produktionskosten.
4. Bearbeitung von "Perilous Summit"
Unter Berücksichtigung all dieser Merkmale ist das Schleifen von Wolframkarbid zweifellos ein gefährlicher Gipfel, den es zu erklimmen gilt. Es stellt extrem hohe Anforderungen an Geräte, Schleifscheiben, Kühlmittel und andere Faktoren. Jedes Glied des Prozesses muss genauestens beachtet werden, sonst sind Schwierigkeiten bei der Bearbeitung vorprogrammiert.
II. Präzisionsnavigation: Der Prozessablauf beim Schleifen von Hartmetall
Angesichts der zahlreichen Herausforderungen beim Schleifen von Hartmetall dient ein wissenschaftlicher und rationeller Prozessablauf als unsere "Navigationskarte", die uns reibungslos zum Erfolg führt.
1. Die Auswahl der richtigen "Allgemein" - Schleifscheibenauswahl
Aufgrund der hohen Härte von Wolframkarbid ist die Auswahl der Schleifscheibe vergleichbar mit der Auswahl fähiger Generäle für eine Schlacht. Schleifscheiben mit mittlerer Härte und guter Verschleißfestigkeit sind die erste Wahl. Materialien wie Korund und Siliziumkarbid sind geeignete Optionen. Außerdem sollten die Korngröße und das Bindemittel der Schleifscheibe flexibel an die jeweiligen Gegebenheiten angepasst werden, um eine optimale Leistung beim Schleifen zu gewährleisten.
2. Einrichten des "Lagers" für das Werkstück - Einspannen des Werkstücks
Die Stabilität des Werkstücks während des Schleifprozesses ist von größter Bedeutung, ähnlich wie Soldaten auf dem Schlachtfeld einen festen Stand benötigen. Geeignete Spannvorrichtungen dienen als "Lager" für das Werkstück und sichern es fest auf der Schleifmaschine. Gleichzeitig sollte die relative Position zwischen dem Werkstück und der Schleifscheibe genau eingestellt werden, um eine solide Grundlage für eine hochpräzise Bearbeitung zu schaffen.
3. Stimmung der "Strings" - Parametereinstellung
Schleifparameter sind wie die Saiten eines Musikinstruments, die sorgfältig eingestellt werden müssen, um eine harmonische Melodie zu erzeugen. Parameter wie Schleiftiefe, Vorschubgeschwindigkeit und Schleifscheibendrehzahl müssen im Hinblick auf die Verarbeitungseffizienz, Qualität und Lebensdauer der Schleifscheibe umfassend berücksichtigt werden. Im Allgemeinen sollte die Schleiftiefe von Hartmetall angemessen reduziert werden, und die Vorschubgeschwindigkeit sollte nicht zu schnell sein, um übermäßigen Schleifscheibenverschleiß und "Verbrennungen" der Werkstückoberfläche zu vermeiden.
4. Begleiten mit "Coolant" - Kühlmittelanwendung
Aufgrund der schlechten Wärmeleitfähigkeit von Wolframkarbid fungiert das Kühlmittel als "Schutzengel" des Werkstücks, indem es dessen Oberflächentemperatur sofort senkt, den Verschleiß der Schleifscheibe minimiert und die Bearbeitungsqualität verbessert. Wasserlösliche und ölbasierte Kühlschmierstoffe werden häufig verwendet und bieten Schutz während des gesamten Schleifprozesses.
5. Während des Prozesses auf der Hut sein - In-Process-Monitoring
Während des Schleifprozesses müssen wir wie Wächter auf einem Aussichtsturm wachsam bleiben und die Abnutzung der Schleifscheibe, die Bearbeitungsqualität des Werkstücks und Temperaturänderungen genau überwachen. Sobald Probleme festgestellt werden, sollten die Schleifparameter umgehend angepasst oder die Schleifscheibe ausgetauscht werden, um einen reibungslosen Ablauf des Prozesses zu gewährleisten.
6. Nachbearbeitung "Mop-Up" - Handhabung nach dem Schleifen
Nach dem Schleifen sollten die nachfolgenden Arbeiten nicht vergessen werden. Reinigung, Inspektion und Verpackung sind wie das Aufräumen des Schlachtfelds, das Zusammenfassen der Ergebnisse nach einer Schlacht. Bei der Reinigung müssen Kühlschmierstoffe und Metallspäne gründlich entfernt werden, um eine Beeinträchtigung der Leistung des Werkstücks zu vermeiden. Die Inspektion sollte streng sein, um sicherzustellen, dass die Qualität des Werkstücks den Anforderungen entspricht. Die Verpackung sollte sorgfältig sein, um das Werkstück während des Transports und der Lagerung vor Schäden zu schützen.
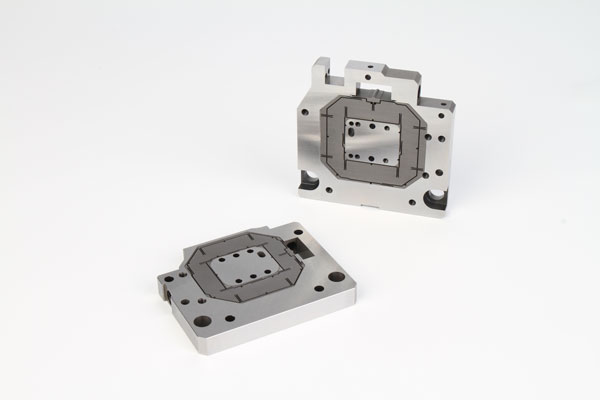
III. Das Eis brechen: Gemeinsame Probleme und Lösungen
Auf der Reise des Wolframkarbidschleifens werden wir zwangsläufig auf einige "versteckte Riffe" stoßen, aber mit den richtigen "Eisbrechertechniken" können wir die Gefahren in Chancen verwandeln.
1. Schleifscheibe "Bruch" - Schneller Scheibenverschleiß
Rascher Schleifscheibenverschleiß ist wie die Waffe eines Soldaten, die vorzeitig bricht und den Bearbeitungszeitplan stark beeinträchtigt. Dies kann durch eine unzureichende Schleifscheibenhärte oder eine falsche Auswahl der Korngröße verursacht werden. In solchen Fällen sollten wir die Schleifscheibe umgehend durch eine mit moderater Härte und geeigneter Korngröße ersetzen und die Schleifparameter anpassen, um die Abnutzungsrate der Schleifscheibe zu verringern und ihr zu ermöglichen, ihre "Schärfe" wiederzuerlangen.
2. Werkstück "Verbrühung" - Oberflächenverbrennungen
Oberflächenverbrennungen am Werkstück sind wie Verbrühungen der Haut und hinterlassen unansehnliche Narben, die die Leistung des Werkstücks beeinträchtigen. Dies wird in der Regel durch zu wenig Kühlmittel oder eine falsche Einstellung der Schleifparameter verursacht. Wir sollten den Kühlmitteldurchsatz erhöhen, um das Werkstück zu "kühlen", und Parameter wie Schleiftiefe, Vorschub und Schleifscheibendrehzahl entsprechend anpassen, um sicherzustellen, dass das Werkstück den Schleifprozess in einer angenehmen "Umgebung" abschließt.
3. Präzision "außerhalb des Ziels" - mangelhafte Bearbeitungsgenauigkeit
Eine unzureichende Bearbeitungsgenauigkeit ist wie ein Pfeil, der sein Ziel verfehlt und die bisherigen Bemühungen zunichte macht. Dies kann durch eine instabile Werkstückspannung, starken Schleifscheibenverschleiß oder eine unangemessene Einstellung der Schleifparameter verursacht werden. Wir sollten die Stabilität der Vorrichtung überprüfen, um eine solide "Position" für das Werkstück zu schaffen, verschlissene Schleifscheiben umgehend austauschen, um ihre "Kampfkraft" wiederherzustellen, und die Schleifparameter optimieren, um die Bearbeitungsgenauigkeit wieder auf Kurs zu bringen.
IV. Eine neue Blaupause für die Zukunft: Zusammenfassung und Ausblick
Das Schleifen von Hartmetallwerkstoffen ist zweifellos ein technisch anspruchsvoller Prozess, der die umfassende Berücksichtigung mehrerer Faktoren erfordert, darunter Materialeigenschaften, Maschinenleistung, Schleifscheibenauswahl und Schleifparameter. Es ist wie das Malen eines komplexen Bildes, bei dem jeder Strich präzise sein muss.
Durch einen angemessenen Prozessablauf und eine strenge prozessbegleitende Überwachung können wir die Bearbeitungsqualität und -effizienz von Hartmetallwerkstücken sicherstellen, so dass Wolframkarbid seinen größeren Wert in der industriellen Produktion entfalten kann. Mit dem kontinuierlichen Fortschritt der Technologie und der Entwicklung neuer Schleiftechnologien wird das Schleifen von Wolframkarbidwerkstoffen eine Ära größerer Effizienz, Präzision und Zuverlässigkeit einläuten. Wir haben allen Grund zu der Annahme, dass Wolframkarbidwerkstoffe in naher Zukunft auf der industriellen Bühne noch heller leuchten werden und der Entwicklung der industriellen Produktion einen stetigen Impuls verleihen.