Tungsten Carbide: The “Unsung Hero” in the Field of Molding Dies
I. Introduction In the sophisticated realm of modern manufacturing, molding dies serve as skilled sculptors, meticulously shaping the form and essence of every product. Tungsten carbide, a low-key yet powerful […]
I. 소개
In the sophisticated realm of modern manufacturing, molding dies serve as skilled sculptors, meticulously shaping the form and essence of every product. Tungsten carbide, a low-key yet powerful “behind-the-scenes hero,” plays a pivotal role in the field of molding dies, thanks to its unique physical and chemical properties. Today, let us unveil the mysterious veil of tungsten carbide in molding dies and explore its indispensable functions.
II. Tungsten Carbide: The Perfect Fusion of Hardness and Toughness
Tungsten carbide, a hard alloy containing up to 3% to 18% tungsten, stands as a marvel bestowed by nature. It boasts extraordinary hardness, coupled with outstanding heat resistance, corrosion resistance, and toughness. Imagine, in the searing heat of a furnace, tungsten carbide remains unyielding, refusing to soften or deform. Under the corrosive onslaught of acids and alkalis, it stands firm, unwavering. Such characteristics make tungsten carbide the material of choice for manufacturing high-precision, high-performance molding dies.
당사의 공장 사업: 초경 부품, 금형 부품, 의료용 사출 금형, 정밀 사출 금형, 테플론 PFA 사출 성형, PFA 튜브 피팅. 이메일: [email protected],whatsapp:+8613302615729.
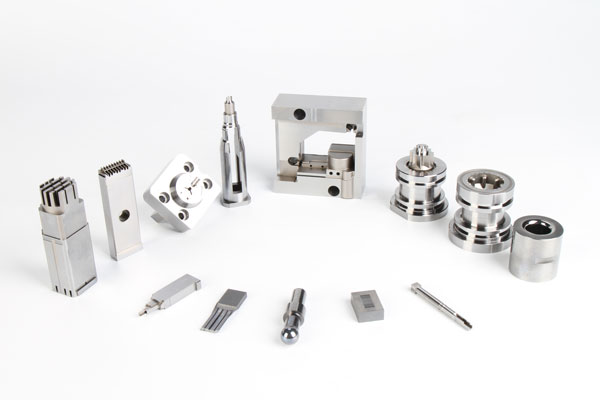
III. Molding Dies: The Art of Precision Manufacturing
Molding dies, the magicians who transform materials like plastics and metals into finished products, operate with wisdom and craftsmanship. From the moment a mold is designed, it is destined to become the cradle of product creation. The upper mold, lower mold, and side mold are each meticulously crafted, ensuring perfection in every detail. Through CNC machining and polishing on machine tools, every aspect of the mold is precisely engineered. Installation, injection molding, stamping, forming, cooling—each step embodies the dedication and ingenuity of craftsmen. Ultimately, when the finished product elegantly emerges from the mold, we cannot help but be captivated by the artistry of precision manufacturing.
IV. Tungsten Carbide: The “Guardian Angel” of Molding Dies
In the arena of molding dies, tungsten carbide undoubtedly shines as the brightest star. Its high hardness and wear resistance provide an impenetrable “armor” for the mold, enabling it to maintain precise dimensions and shapes over extended periods of use, ensuring high precision and stability of the product. Heat resistance and corrosion resistance allow tungsten carbide molds to operate stably in high-temperature and highly corrosive environments, significantly enhancing production efficiency. Moreover, its excellent toughness prevents cracks and fractures, extending the mold’s service life. Notably, the broad applicability of tungsten carbide molds enables them to effortlessly handle plastics, metals, rubbers, glasses, and more, making them a versatile “jack-of-all-trades” in the manufacturing industry.
Specifically, in the field of metal processing, tungsten carbide molds, with their precise dimensions and robust compressive strength, assist manufacturers in achieving accurate forming in processes such as metal stamping, casting, and forging. In the realm of plastic injection molding, tungsten carbide molds withstand the rigors of high pressure and temperature, swiftly and accurately manufacturing various plastic products. Similarly, in rubber manufacturing and glass forming, tungsten carbide molds provide robust support for product processing with their high hardness and wear resistance.
V. 결론
In summary, the role of tungsten carbide in molding dies is undeniable. With its unique performance advantages, it injects powerful vitality into molding dies. As the manufacturing industry continues to upgrade and develop, the application prospects of tungsten carbide in the field of molding dies will become even broader. Let us eagerly anticipate this “unsung hero” shining even more brightly on the future stage of the manufacturing industry!