Causes of Deformation in Tungsten Carbide Products and Corresponding Countermeasures
I. Introduction Tungsten carbide, renowned for its exceptional hardness, high strength, excellent wear resistance, and good thermal stability, holds a pivotal position in fields such as cutting tools, precision molds, […]
I. Introduction
Tungsten carbide, renowned for its exceptional hardness, high strength, excellent wear resistance, and good thermal stability, holds a pivotal position in fields such as cutting tools, precision molds, and wear-resistant components. However, during the manufacturing and application processes of tungsten carbide products, deformation issues frequently arise, which not only compromise product performance and service life but may also pose potential threats to production safety. Therefore, delving into the root causes of deformation in tungsten carbide products is of paramount importance for enhancing product quality and optimizing production processes.
II. Multi-dimensional Analysis of the Causes of Deformation in Tungsten Carbide Products
1. Carbon Gradient Effect
During the intricate manufacturing process of tungsten carbide, critical stages such as dewaxing, pre-sintering, and sintering can induce subtle variations in the product’s carbon content, leading to the formation of a carbon gradient within the tungsten carbide. Particularly in an H2 sintering atmosphere, if the concentration of CXHY compounds exceeds the optimal level or the carbon content in the filler is excessive, large, elongated, or flat-shaped products may experience uneven “decarburization” and “carburization” across different sections. This disparity results in varying degrees and sequences of shrinkage, ultimately causing product deformation and bending.
Our factory business: carbide parts, mold parts, medical injection molds, precision injection molds, teflon PFA injection molding, PFA tube fittings. email: [email protected],whatsapp:+8613302615729.
2. Cobalt Gradient Influence
In the vacuum sintering process, the wettability of cobalt on the surface of graphite boats emerges as a pivotal factor influencing product morphology. When the wettability is poor, cobalt liquid migrates upwards, increasing the surface tension on the upper surface of the product and decreasing it on the lower surface, leading to upward convexity. Conversely, when the wettability is good, cobalt liquid migrates downwards, increasing the surface tension on the lower surface of the alloy and causing downward concavity. Both scenarios result in deformation of the tungsten carbide product.
3. Impact of Temperature Gradient
During the sintering process, cobalt, upon melting under heat, tends to flow towards high-temperature regions, resulting in an increased cobalt content in these areas of the product and the formation of a cobalt gradient. The greater the temperature gradient, the more uneven the cobalt distribution, exacerbating product deformation.
4. Press Product Density Gradient
In the pressing stage of tungsten carbide, factors such as force attenuation, uneven material loading, and complex product shapes can lead to variations in the loose bulk density of the mixed material, forming a press product density gradient. Sections with higher density experience less shrinkage, while those with lower density undergo greater shrinkage, thereby causing product deformation and bending.
5. Other Potential Factors
In addition to the aforementioned factors, improper boat loading, differences in shrinkage coefficients, excessive use, and exposure to extreme environmental conditions (such as high temperatures or humidity) may also contribute to the deformation of tungsten carbide products.
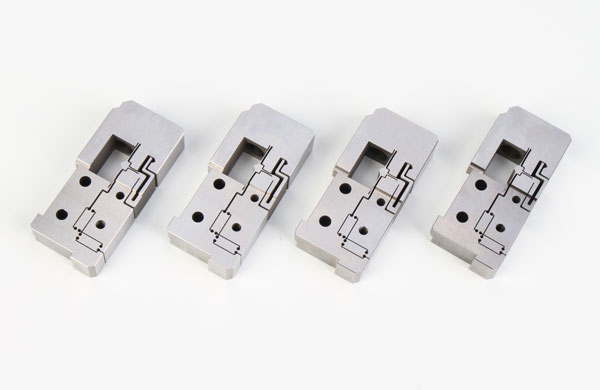
III. Comprehensive Countermeasures for Deformation in Tungsten Carbide Products
1. Process Optimization and Innovation
By finely adjusting the sintering atmosphere, strictly controlling the addition of carbon and cobalt, and improving the pressing process, the impact of carbon gradients, cobalt gradients, and temperature gradients on product deformation can be effectively mitigated.
2. Strengthening the Quality Control System
Strictly monitor the quality of raw materials to ensure uniform content and distribution of key elements such as carbon and cobalt, thereby reducing the risk of product deformation from the source.
3. Scientific Design of Product Structure
Optimize product design to reduce shape complexity and asymmetry, thereby lowering the risk of deformation during the manufacturing process.
4. Rational Use and Maintenance
Avoid excessive use or exposure to extreme environmental conditions during the application process. Simultaneously, conduct regular product maintenance and inspections to promptly identify and address potential deformation issues.
IV. Conclusion
The deformation of tungsten carbide products is a complex issue influenced by multiple factors. By conducting an in-depth analysis of key factors such as carbon gradients, cobalt gradients, temperature gradients, and press product density gradients, and adopting targeted countermeasures based on actual production conditions, the deformation issues of tungsten carbide products can be effectively reduced, thereby enhancing product quality and production efficiency. Looking ahead, with the continuous advancement of technology and the ongoing optimization of processes, the deformation problems of tungsten carbide products are bound to be better resolved in the future.