Comparative Analysis of Tungsten Carbide and Pure Tungsten
I. Introduction In the realm of industrial materials, tungsten carbide and pure tungsten, though both derived from the element tungsten, exhibit distinct physical and chemical properties due to differences in […]
I. Introduction
In the realm of industrial materials, tungsten carbide and pure tungsten, though both derived from the element tungsten, exhibit distinct physical and chemical properties due to differences in composition and processing. This article provides a systematic analysis of their core distinctions from a materials science perspective, offering a scientific basis for engineering material selection.
II. Composition and Structure: The Essence of Alloys vs. Pure Metals
Tungsten Carbide
As a typical cemented carbide, tungsten carbide is produced through powder metallurgy, sintering tungsten carbide (WC) and cobalt (Co) or other metallic binders at high temperatures and pressures. Its microstructure consists of a dual-phase system: 85%-95% WC hard phase (grain size 0.2-10 μm) imparting high hardness and wear resistance, and a Co-based binder phase enhancing toughness through metallic bonding, achieving a balance of “hardness without brittleness.”
Our factory business: carbide parts, mold parts, medical injection molds, precision injection molds, teflon PFA injection molding, PFA tube fittings. email: [email protected],whatsapp:+8613302615729.
Pure Tungsten
With the chemical symbol W (atomic number 74), pure tungsten metal requires ≥99.95% purity. Its body-centered cubic (BCC) crystal structure features an atomic spacing of 0.274 nm, resulting in a theoretical density of 19.25 g/cm³ (measured 19.3 g/cm³) and an ultra-high melting point of 3422℃. This elemental metal exhibits extreme hardness (69 HRA) coupled with significant brittleness.
III. Hardness and Properties: The Art of Balancing Rigidity and Toughness
Hardness Comparison
Pure tungsten achieves a Rockwell hardness (HRA) of 69, approaching diamond levels, but its high hardness is accompanied by pronounced brittleness. Tungsten carbide, while slightly lower in hardness (HRA 89-94 depending on WC particle size), leverages the Co binder to enhance toughness, with flexural strength reaching 2000-3500 MPa—far surpassing pure tungsten’s brittle fracture characteristics.
Comprehensive Performance
- Pure Tungsten: Maintains strength at 2000℃, with a thermal expansion coefficient of 4.5×10⁻⁶/℃, and exceptional acid/alkali corrosion resistance, though prone to microcracking during processing.
- Tungsten Carbide: Exhibits 8-20x higher wear resistance than tool steels, with heat resistance up to 800-1000℃. Through compositional adjustments (e.g., adding TiC, TaC), red hardness can be further optimized, balancing hardness and toughness.
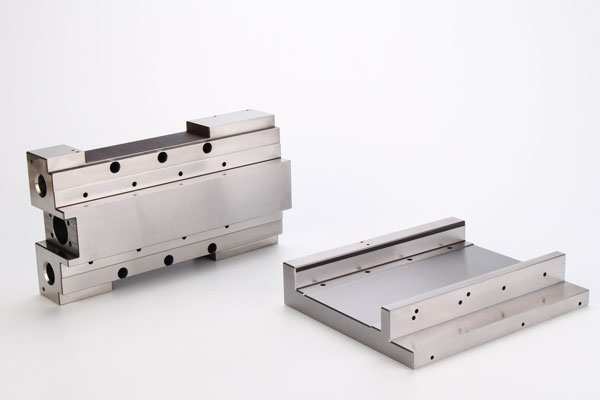
IV. Application Domains: From Cutting Tools to Strategic Materials
Tungsten Carbide Applications
- Machining: Accounts for 65% of global cemented carbide production, used in drills, milling cutters, turning tools, etc., with tool life 5-10x longer than high-speed steels.
- Precision Manufacturing: Employed in stamping dies, cold heading dies (surface roughness Ra0.05μm), and aerospace components like engine nozzles and gyroscopes for high-temperature resistance.
Strategic Value of Pure Tungsten
- High-End Equipment: Utilized in spacecraft propulsion system electrodes, nuclear reactor neutron shielding layers, relying on its high density (19.3 g/cm³) and radiation resistance.
- Specialty Devices: X-ray tube targets, vacuum furnace heating elements, leveraging its high-temperature stability and electron emission capabilities.
V. Processing and Cost: Practical Considerations in Industrial Production
Processing Characteristics
Pure tungsten, due to its high hardness and low fracture toughness, requires non-traditional methods like wire electrical discharge machining (WEDM) and laser processing, with costs 3-5x higher than tungsten carbide. Tungsten carbide can be machined via conventional turning and grinding, achieving surface precision of ±0.005mm.
Economic Analysis
- Raw Material Costs: Pure tungsten ~400-600 RMB/kg; tungsten carbide raw materials (WC powder + Co powder) ~150-250 RMB/kg.
- Manufacturing Costs: Tungsten carbide achieves >95% material utilization through powder metallurgy near-net shaping; pure tungsten processing waste rates reach 30%-50%.
VI. Conclusion: The Dialectics of Material Selection
The differentiated characteristics of tungsten carbide and pure tungsten define their irreplaceable roles: tungsten carbide dominates machining and precision manufacturing with its “hard yet tough” properties, while pure tungsten excels in high-end equipment and specialty materials through “extreme hardness and stability.” In engineering practice, material selection must align with operational conditions (e.g., temperature, pressure, corrosion) and performance requirements (e.g., wear resistance, toughness, precision). For instance, aircraft engine blade coatings often employ composite solutions combining tungsten carbide substrates with pure tungsten coatings for high-temperature resistance and oxidation protection, while semiconductor etching equipment electrodes rely on pure tungsten’s ultra-high purity and electronic properties.
Professional Support
Dongguan Yize Mold, a seasoned tungsten carbide processing service provider, offers customized tungsten carbide mold components, precision part machining, and turnkey solutions. Contact us at +86 13302615729 (WeChat/WhatsApp) for technical consultations and product quotations.