Comprehensive Analysis of Tungsten Carbide Product Deformation
Tungsten carbide, renowned as the “industrial tooth” for its ultra-high hardness, exceptional wear resistance, and superior thermal stability, dominates precision manufacturing sectors. However, deformation issues during production—such as warping, bending, […]
Tungsten carbide, renowned as the “industrial tooth” for its ultra-high hardness, exceptional wear resistance, and superior thermal stability, dominates precision manufacturing sectors. However, deformation issues during production—such as warping, bending, or dimensional instability—not only compromise product quality and performance but also threaten production efficiency and safety. This article dissects the root causes of deformation from microscopic material behaviors to macroscopic process control, offering actionable solutions for manufacturers.
I. Carbon Gradient Imbalance: The “Molecular Civil War” During Sintering
During dewaxing, presintering, and sintering, carbon content fluctuations create concentration gradients within tungsten carbide products. When H₂ sintering atmosphere CₓHᵧ compounds exceed 1.2% (vol.) or filler carbon content surpasses 0.8% (wt.), large/elongated components exhibit uneven decarburization/carburization, forming carbon gradients.
Our factory business: carbide parts, mold parts, medical injection molds, precision injection molds, teflon PFA injection molding, PFA tube fittings. email: [email protected],whatsapp:+8613302615729.
- Mechanism: High-carbon zones (≥6.2% C) solidify last, while low-carbon zones (≤5.8% C) freeze first. Liquid cobalt migrates toward pre-solidified regions under shrinkage stress, causing:
- Elongated products: Concave high-carbon surfaces and convex low-carbon surfaces (deformation rate up to 0.3 mm/m).
- Case Study: A mold manufacturer reduced rework costs by 20% after optimizing filler carbon content to maintain a ±0.1% C gradient.
II. Cobalt Migration Disorder: The “Gravitational Battle” of Liquid Metal
Cobalt’s wetting behavior on graphite boats dictates its redistribution during vacuum sintering:
- Upward Migration: Poor wetting (contact angle >90°) causes cobalt to accumulate on upper surfaces, creating convexity.
- Downward Migration: Excessive wetting (contact angle <30°) drives cobalt sinking, resulting in concavity.
- Technical Breakthrough: Boron nitride-coated boats reduced cobalt migration by 67% in a precision component factory.
III. Thermal Gradient Disruption: The “Thermodynamic Trap” in Furnaces
Temperature differentials >100°C amplify cobalt concentration gradients by 15%, accelerating deformation. Key control measures include:
- Furnace Optimization: Multi-zone temperature control (±5°C accuracy) using infrared thermal imaging + AI algorithms.
- Loading Strategy: Minimize part spacing to <5 mm to reduce thermal shadowing.
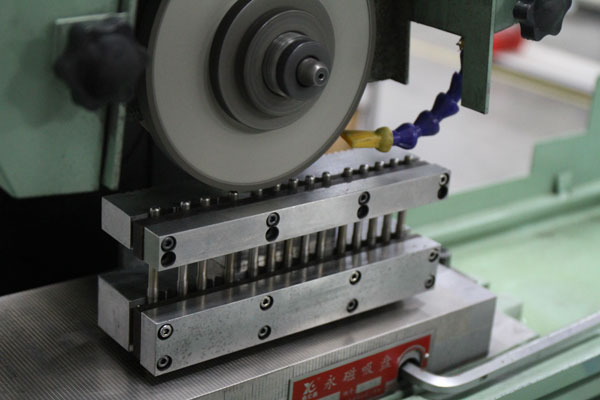
IV. Density Gradient Pitfalls: The “Invisible Landmines” of Compaction
Compaction forces decaying by 30% over 100 mm, uneven powder filling, and complex geometries create density gradients (Δρ=0.1 g/cm³ → Δshrinkage=0.05 mm). Solutions:
- Isostatic Pressing: Achieves ±0.02 g/cm³ density uniformity.
- Hybrid Compaction: Segmented pre-pressing + final forming for complex parts.
V. Hidden Culprits: The “Detail Devils” Neglected in Production
- Improper Boat Loading: Angular deviations >3° induce stress concentrations.
- CTE Mismatch: Thermal expansion coefficient differences >2×10⁻⁶/°C between WC and fixtures cause residual stress.
- Thermal Conductivity Limitations: WC’s 30 W/m·K (vs. steel’s 150 W/m·K) exacerbates thermal shock risks.
VI. Systemic Solutions: End-to-End Process Reinvention
Problem Dimension | Solution Framework | Performance Gains |
---|---|---|
Carbon Gradient | Dynamic carbon potential monitoring + gradient decarburization-carburization hybrid process | 80% reduction in carbon gradient variability |
Cobalt Migration | Nano-encapsulated cobalt alloys to reduce liquid metal activity | 75% suppression of cobalt migration |
Thermal Gradient | AI-driven infrared thermal mapping with real-time power adjustment | ±3°C temperature uniformity |
Density Gradient | 3D-printed preforms for spatial density control | ±0.01 g/cm³ density precision |
Process Governance | Five-dimensional traceability system (raw material → compaction → sintering → machining → inspection) | Product yield increased from 78% to 95% |
Conclusion
Tungsten carbide deformation stems from the synergistic effects of material physics, process parameters, and equipment precision. Breakthroughs in material genome engineering, smart sintering technologies, and digital twin systems enable the transition from empirical trial-and-error to data-driven precision manufacturing.
Act Now to Upgrade Your Quality
📞 Technical Consultation: +86 13302615729 (WeChat/WhatsApp)
📍 Headquarters: No. 162, Zhen’an East Road, Xiao’bian Community, Chang’an Town, Dongguan City, Guangdong Province
Engage with Us
Have you encountered deformation challenges in tungsten carbide products? Share your pain points in the comments for a FREE technical diagnosis!