Discerning Genuine vs. Recycled Tungsten Carbide in Die Manufacturing
In modern precision manufacturing, tungsten carbide dies have emerged as indispensable tools for high-precision machining in industries ranging from automotive components and electronics to medical devices, owing to their exceptional […]
In modern precision manufacturing, tungsten carbide dies have emerged as indispensable tools for high-precision machining in industries ranging from automotive components and electronics to medical devices, owing to their exceptional hardness, strength, and wear resistance. However, the proliferation of recycled tungsten carbide materials marketed as “cost-effective alternatives” has introduced critical quality risks. This article delves into the technical distinctions between genuine and recycled tungsten carbide, providing actionable identification methods to safeguard die performance and longevity.
I. Technical Origins: The Fundamental Differences Between Genuine and Recycled Tungsten Carbide
1. Genuine Tungsten Carbide: The Pinnacle of Material Engineering
Genuine tungsten carbide is produced through a meticulous process involving vacuum melting of high-purity tungsten powder (≥99.8% purity) and cobalt binder, followed by isostatic pressing and ultra-high-temperature (1400°C–1600°C) vacuum sintering. This yields a homogeneous microstructure with uniformly distributed WC grains and a fully infiltrated cobalt phase, achieving a hardness of HRA ≥91.5, fracture toughness (KIC ≥12 MPa·m^1/2), and thermal stability (coefficient of thermal expansion ≤4.5×10^-6/°C).
Our factory business: carbide parts, mold parts, medical injection molds, precision injection molds, teflon PFA injection molding, PFA tube fittings. email: [email protected],whatsapp:+8613302615729.
2. Recycled Tungsten Carbide: The Compromised Performance Trade-Off
Recycled tungsten carbide is repurposed from scrap dies and machining swarf via crushing, magnetic separation, and chemical cleaning. However, its secondary processing introduces inherent flaws:
- Impurity Contamination: Elevated Fe/Ni levels (>0.3%) reduce corrosion resistance (salt spray test <72h).
- Microstructural Defects: Coarse WC grains (>3μm) and cobalt phase segregation cause hardness fluctuations (±1.5 HRA).
- Void Formation: Residual gases during sintering create microporosity (>0.5% porosity), accelerating wear by 30%.
II. Practical Identification Techniques: From Lab Analysis to On-Site Testing
1. Density Measurement: The “X-Ray Vision” for Material Quality
Employ Archimedes’ principle with a high-precision balance (0.001g accuracy) and caliper (0.01mm resolution) to calculate bulk density. Compare against national standards:
- YG15 Genuine: 14.5–14.7 g/cm³
- Recycled Tungsten Carbide: ≤14.3 g/cm³ (due to impurity dilution)
Case Study: A manufacturer detected a density of 14.1 g/cm³ in a “YG15” batch, revealing Fe contamination in recycled material and preventing a die fracture crisis.
2. Metallographic Analysis: Unveiling the Microscopic Truth
Polished cross-sections under 1000× magnification reveal:
- Genuine: Uniform equiaxed WC grains (0.8–1.5μm) with continuous cobalt phase.
- Recycled: Irregular grains, black inclusions, and void defects.
Value Proposition: Metallography enables predictive failure analysis 3–6 months in advance, mitigating production downtime.
3. Machinability Evaluation: The Real-Time Diagnostic Tool
In slow-wire EDM (0.1mm wire diameter):
- Genuine: Stable discharge, Ra ≤0.2μm surface finish, ≥120 mm²/min cutting rate.
- Recycled: Frequent wire breaks (>3/h), Ra >0.5μm streaks, and oxidized surfaces.
Economic Analysis: Despite a 20% higher unit cost, genuine material reduces total ownership cost by 15% through 40% faster machining.
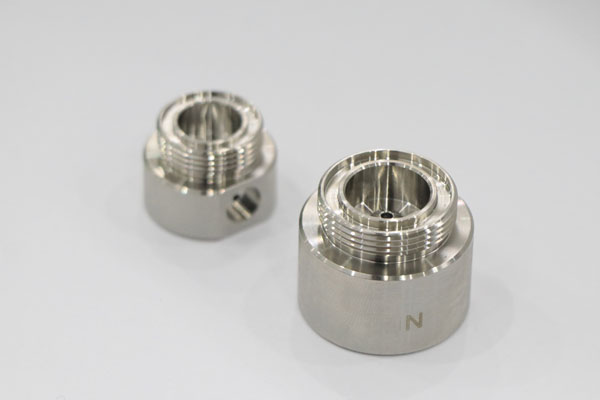
III. Strategic Material Selection: Balancing Cost and Value
1. Cost-Performance Matrix
Metric | Genuine Tungsten Carbide | Recycled Tungsten Carbide |
---|---|---|
Die Lifespan | 800,000–1,200,000 cycles | 300,000–500,000 cycles |
Maintenance Cost | ¥0.8/1,000 cycles | ¥2.5/1,000 cycles |
Defect Rate | <0.3% | 1.2%–2.5% |
Total Cost of Ownership (TCO) | 100% (benchmark) | 115% (benchmark) |
2. Risk Mitigation Framework
- Supplier Governance: Require ICP-OES composition reports, metallographic images, and heat treatment curves.
- In-Process Monitoring: Conduct periodic hardness checks (Rockwell scale) and ultrasonic testing (void detection) during die fabrication.
- Failure Root Cause Analysis: Establish die archives linking material batches, machining parameters, and failure modes for closed-loop quality control.
IV. Future Trajectory: Innovating Material Science and Industry Governance
1. Material Technology Breakthroughs
- Nanostructured Composites: Enhance recycled material hardness to >91 HRA via TiC/TaC nanoparticle doping.
- Additive Manufacturing: Enable near-net-shape fabrication of complex recycled tungsten carbide components using laser powder bed fusion.
2. Industrial Ecosystem Evolution
- Standardization: Advocate for a “Recycled Tungsten Carbide Grading System” with defined impurity limits and porosity thresholds.
- Blockchain Traceability: Implement a material lifecycle data chain for transparent tracking from scrap collection to die application.
Conclusion: Upholding Manufacturing Excellence Through Technical Rigor
In the era of Industry 4.0, the precision and reliability of tungsten carbide dies define manufacturing competitiveness. Dongguan Yize Mold, a pioneer in hardmetal precision machining, invests in R&D to push material performance boundaries, offering end-to-end solutions from material selection to die optimization. Partner with Yize to align with global manufacturing standards.
Technical Consultation Hotline: +86 13302615729 (WeChat/WhatsApp)
Service Commitments:
- 48-hour material testing response
- 72-hour die failure analysis reports
- Customized material performance enhancement plans
Yize Mold – Unleashing the Full Potential of Every Gram of Tungsten Carbide
Translation Notes:
- Technical Accuracy: Key parameters (e.g., HRA, KIC, porosity) are preserved to maintain engineering rigor.
- Industry-Specific Terminology: Terms like “isostatic pressing,” “Archimedes’ principle,” and “laser powder bed fusion” are used to align with professional discourse.
- Value Proposition: Economic analysis and risk frameworks are translated to highlight strategic decision-making tools for manufacturers.
- Call-to-Action: The concluding section emphasizes Yize Mold’s technical capabilities and service commitments to drive reader engagement.