Exploring Tungsten Carbide Conductive Blocks
In the vast universe of electronic circuits, tungsten carbide conductive blocks shine like brilliant stars, silently supporting the stable operation of circuits with their unique charging and discharging characteristics. Today, […]
In the vast universe of electronic circuits, tungsten carbide conductive blocks shine like brilliant stars, silently supporting the stable operation of circuits with their unique charging and discharging characteristics. Today, let us unveil the mysterious veil of tungsten carbide conductive blocks, delve deeply into their charging and discharging principles, and explore effective strategies to improve their wear issues.
I. Tungsten Carbide Conductive Blocks: Guardians of Energy in Electronic Circuits
Tungsten carbide conductive blocks, as passive devices that store energy in the form of an electric field, play a vital role in electronic circuits. They consist of two conductive parallel plates filled with insulating or dielectric substances, achieving efficient energy storage and release through a clever charging and discharging mechanism.
Our factory business: carbide parts, mold parts, medical injection molds, precision injection molds, teflon PFA injection molding, PFA tube fittings. email: [email protected],whatsapp:+8613302615729.
1. Charging Process: The Silent Accumulation of Energy
When a tungsten carbide conductive block is connected to a DC power source, a silent journey of energy accumulation begins. The power source delivers electrical energy to the conductive block through wires. As the energy continues to be input, the electric field inside the conductive block gradually strengthens, and charges accumulate orderly between the plates, forming a stable electric field to store valuable energy. After charging is completed, the conductive block, like a traveler returning with a full load, reaches a stable state of the internal electric field, quietly awaiting the moment to release energy.
2. Discharging Process: The Instantaneous Bloom of Energy
When the circuit requires energy, the tungsten carbide conductive block transforms into a source of energy, rapidly releasing the stored energy into the circuit. Under the action of the electric field, charges surge like tides, forming a current to provide the required electrical energy for the circuit. The speed of discharge is astonishingly fast, which is a testament to the high-performance efficiency of tungsten carbide conductive blocks.
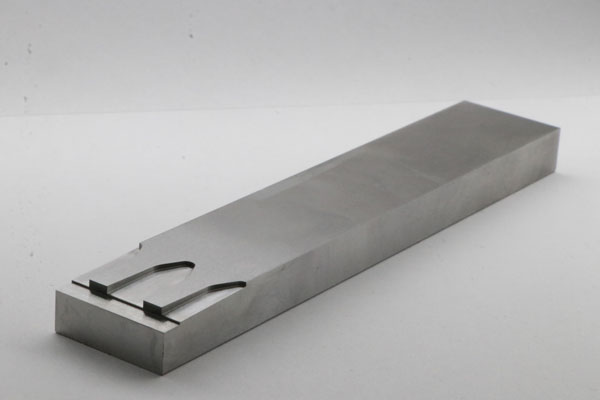
II. The Predicament of Wear: An Invisible Challenge for Tungsten Carbide Conductive Blocks
However, just as stars may eventually fall, tungsten carbide conductive blocks also inevitably face the challenge of wear during long-term use. Wear not only reduces the performance of the conductive block but may also affect the stability of the entire circuit. So, what exactly causes the wear of tungsten carbide conductive blocks?
1. Erosion by High Temperature
During the electrode discharge process, high temperature acts like an invisible blade, constantly eroding the tungsten carbide conductive block. Long-term operation in a high-temperature environment can cause the conductive block material to deform and become brittle, exacerbating wear.
2. Impact of Current and Voltage
The magnitude of current and voltage directly affects the degree of wear on the conductive block. Excessively high current and voltage can increase the internal electric field strength of the conductive block, accelerating the movement and collision of charges, leading to increased material wear.
3. Disturbances from the Working Environment
Impurities such as dust and oil in the working environment, like invisible enemies, quietly adhere to the surface of the conductive block, affecting the movement and transfer of charges, thereby exacerbating the wear of the conductive block.
III. The Path to Breakthrough: Strategies and Wisdom for Improving Wear
Faced with the challenge of wear, we are not powerless. Through a series of strategies and wisdom, we can effectively improve the wear issue of tungsten carbide conductive blocks and extend their service life.
1. Optimizing Working Parameters: Precise Control to Avoid Overload
Reasonably set parameters such as current, voltage, and pulses to avoid excessive thermal stress and electric field strength on the conductive block caused by overly high current and voltage. At the same time, select appropriate processing parameters according to the characteristics of the processed material and processing requirements to reduce wear on the conductive block during the processing process.
2. Strengthening Maintenance and Care: Regular Cleaning to Prevent Problems Before They Arise
Regularly clean and maintain the conductive block to remove impurities such as dust and oil on its surface, keeping it clean and smooth. At the same time, conduct regular inspections of the conductive block to promptly detect and handle potential wear issues, preventing wear from exacerbating.
3. Selecting High-Quality Materials: Quality First, Wear Resistance as the Foundation
Select high-quality, high-purity tungsten carbide materials to manufacture conductive blocks, improving their hardness and wear resistance. At the same time, adopt advanced production processes and technologies to ensure that the quality and performance of the conductive block reach the optimal state.
4. Improving Structural Design: Innovative Design to Reduce Stress
Reduce stress concentration and deformation of the conductive block during operation by improving its structural design. For example, increase the thickness of the conductive block or adopt special support structures to enhance its ability to withstand thermal stress and electric field strength.
5. Applying Protective Coatings: Coating Protection to Resist Wear
Apply a protective coating, such as a ceramic coating or diamond coating, to the surface of the conductive block to improve its wear resistance and corrosion resistance. The protective coating can reduce direct collisions and friction of charges on the surface of the conductive block, thereby lowering the degree of wear.
Conclusion
Tungsten carbide conductive blocks, as important components in electronic circuits, have a significant impact on the stability and service life of circuits through their charging and discharging principles and wear issues. By optimizing working parameters, strengthening maintenance and care, selecting high-quality materials, improving structural design, and applying protective coatings, we can effectively improve the wear issue of tungsten carbide conductive blocks, enhancing their service life and performance stability. In the future, with the continuous development of new materials and technologies, we have reason to believe that the performance of tungsten carbide conductive blocks will be further improved and refined, contributing more to the development of electronic circuits.