Guide to Selecting Precision Tungsten Carbide Molds
In the field of precision machining in manufacturing, molds serve as the “mother of industrial production,” directly determining production efficiency and product quality. Tungsten carbide molds, with their high hardness […]
In the field of precision machining in manufacturing, molds serve as the “mother of industrial production,” directly determining production efficiency and product quality. Tungsten carbide molds, with their high hardness (HRA≥90), wear resistance (ten times that of ordinary steel), and thermal stability (maintaining hardness at 600°C), have become the preferred choice in high-end manufacturing sectors such as electronics, automotive, and medical industries. Faced with a plethora of products in the market, how can enterprises make precise selections? This article systematically analyzes selection strategies from six key dimensions.
I. Decoding Core Parameters of Tungsten Carbide Materials: The Triangular Balance of Hardness, Toughness, and Wear Resistance
Tungsten carbide (hardmetal) consists of tungsten carbide (WC) and a cobalt (Co) binder phase, with its properties determined by the composition ratio and microstructure:
Our factory business: carbide parts, mold parts, medical injection molds, precision injection molds, teflon PFA injection molding, PFA tube fittings. email: info@yizemould.com,whatsapp:+8613302615729.
- Hardness Gradient: Ultra-fine grain tungsten carbide (WC particle size <0.4μm) can achieve a hardness of HRA93, suitable for precision stamping molds.
- Toughness Index: With a Co content of 10%-15%, the flexural strength reaches 3000MPa, balancing wear resistance and impact resistance.
- Wear Mechanism: WC crystals form an oxide film during friction, reducing the wear rate to 0.01mm³/km.
When purchasing, request material test reports, focusing on:
- Dual indicators of Rockwell hardness (HRA) and Vickers hardness (HV).
- Fracture toughness (KIC) ≥15MPa·m¹/².
- Coefficient of thermal expansion (CTE) ≤5×10⁻⁶/°C.
II. Precision Matching Principles: Stepwise Selection from ±0.005mm to ±0.1mm
Select the corresponding mold precision grade based on product tolerance zones:
Product Precision Grade | Mold Manufacturing Tolerance | Applicable Fields | Typical Cases |
---|---|---|---|
IT5 | ±0.005mm | Semiconductor packaging molds | 0201 package chip forming molds |
IT7 | ±0.015mm | Precision connector molds | Type-C interface stamping molds |
IT9 | ±0.05mm | Automotive parts molds | Brake pad stamping molds |
When verifying precision, require the supplier to provide:
- Coordinate Measuring Machine (CMM) reports.
- Mold cavity profile measurement data.
- CPK values (≥1.33) for trial mold part size distribution.
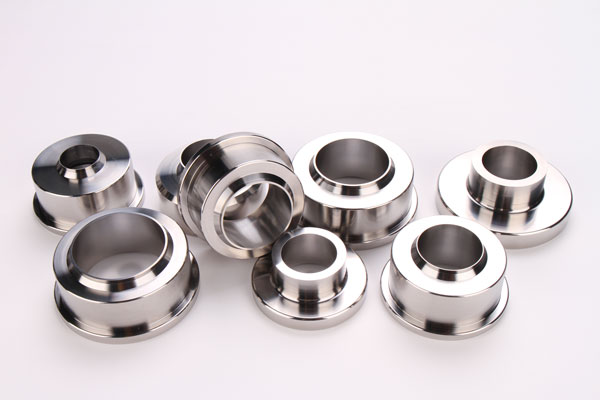
III. Lifespan Prediction Model: Strategies for Doubling Lifespan from Materials to Processes
Mold lifespan is influenced by four major factors:
- Material Fatigue: Gradient sintering processes can improve thermal crack resistance by 30%.
- Wear Mechanisms: PVD coatings (TiAlN) can reduce the friction coefficient to 0.3.
- Thermal Stress: Hot isostatic pressing eliminates internal residual stress.
- Operating Conditions: Every 100°C increase in operating temperature reduces lifespan by 15%.
When assessing lifespan, obtain:
- Mold lifespan test data under the same operating conditions (strokes per hour).
- Heat treatment process curves (quenching temperature ±5°C).
- Surface treatment layer thickness test reports (≥3μm).
IV. Total Lifecycle Cost Analysis: Optimal Solutions from a TCO Perspective
Construct a Total Cost of Ownership (TCO) model:
TCO = Mold Purchase Price + (Maintenance Cost × Usage Cycle) + (Downtime Loss × Failure Incidents) - Residual Value
Case Comparison:
- High-end mold: Unit price 150,000 yuan, lifespan 500,000 mold cycles, TCO=0.35 yuan/mold cycle.
- Ordinary mold: Unit price 80,000 yuan, lifespan 150,000 mold cycles, TCO=0.62 yuan/mold cycle.
Decision-Making Suggestions:
- When annual production >1 million pieces, prioritize high-lifespan molds.
- For budget constraints, consider a “basic model + local coating” combination solution.
V. Supplier Capability Assessment: Dual Certification of Technical Strength and Service System
Quality suppliers should possess:
- R&D Capabilities: Equipped with material laboratories (featuring SEM, XRD testing equipment).
- Manufacturing Systems: Certified with ISO 9001 + IATF 16949.
- Service Networks: 24-hour response mechanism + mold repair centers.
- Data Traceability: Provide full-process records from raw material batches to delivery.
Key Inspection Points:
- Request a visit to the production workshop (focus on constant temperature and humidity processing areas).
- Verify typical customer cases (especially in the same industry).
- Test technical support response speed (simulate emergency failure scenarios).
VI. Practical Selection Guide: Five Steps to Secure Quality Molds
- Demand Diagnosis: Create a product tolerance zone distribution map, clarifying key dimensions.
- Technical Benchmarking: Develop a supplier technical parameter comparison matrix.
- Sample Verification: Request three rounds of trial mold parts and test dimensional stability.
- Contractual Constraints: Clarify mold lifespan commitments and compensation clauses.
- Continuous Optimization: Establish a mold usage database and regularly review improvements.
Conclusion
The selection of precision tungsten carbide molds is essentially an art of balancing technical and economic factors. Enterprises need to establish a scientific evaluation system, aligning with product strategic positioning, to find the optimal solution between performance, cost, and risk. Remember: mold investment is not just equipment procurement but a strategic upgrade of manufacturing capabilities. Through systematic selection, enterprises can transform mold costs into quality advantages, gaining an edge in fierce market competition.