How to Select Tungsten Carbide Punches and Pins?
I. Tungsten Carbide Punches & Pins: The Material Science Behind Unmatched Performance Tungsten carbide (WC-Co composites), crafted via powder metallurgy with cobalt (Co) as the binder, achieves hardness (HRA 85-92), compressive […]
I. Tungsten Carbide Punches & Pins: The Material Science Behind Unmatched Performance
Tungsten carbide (WC-Co composites), crafted via powder metallurgy with cobalt (Co) as the binder, achieves hardness (HRA 85-92), compressive strength (≥4,000 MPa), and high-temperature resistance (unsoftened at 1,000°C). Its wear resistance outperforms tool steel by 8-12 times, making it indispensable in industries like 3C electronics (micro-punching), automotive (thick-plate blanking), and precision metal forming (e.g., stainless steel casings for mobile phones).
II. Golden Rules for Selection: A Three-Dimensional Approach
1. Material Compatibility: Balancing Hardness and Toughness
Our factory business: carbide parts, mold parts, medical injection molds, precision injection molds, teflon PFA injection molding, PFA tube fittings. email: [email protected],whatsapp:+8613302615729.
- High-hardness materials (e.g., stainless steel, titanium alloys):
Require HRA 88-90 tungsten carbide grades (≤6% Co) like YG15X or CD650 to prevent brittle fracture. - Medium/low-hardness materials (e.g., copper, aluminum, galvanized steel):
Opt for tougher grades (8-10% Co) like YG8 or CD-KR887 to reduce chipping risks. - Ultra-thick plates (>5mm):
Adopt gradient-structured tungsten carbide (hard surface layer + tough core) or vacuum-hardened+deep-cryogenic-treated tools for shock resistance.
2. Process Requirements: Triangle Trade-offs of Precision, Speed, and Lifespan
- Ultra-precision punching (tolerance ≤±0.005mm):
Use mirror-polished (Ra≤0.1μm) tungsten carbide with TiN or DLC coatings (friction coefficient ≤0.1). - High-speed continuous punching (>300 SPM):
Prioritize nano-crystalline grades with ruthenium (Ru) additives (e.g., CD-KR466) for 20% improved red-hardness and 3x longer lifespan. - Complex-shape punching (e.g., micro-holes, narrow slots):
Customize tools with laser-cladded edges and self-lubricating grooves to mitigate material sticking.
3. Cost Optimization: Balancing Upfront Investment vs. Long-Term Gains
- Cost-effective solution (small/medium batches):
Domestic premium tungsten carbide + vacuum heat treatment (40% lower cost vs. imports, 200,000+ cycles). - Long-lifespan solution (high-precision scenarios):
Ultra-fine-grain imported tungsten carbide + PVD multi-layer coatings (30% higher initial cost, 5-8x longer lifespan, 65% lower unit cost).
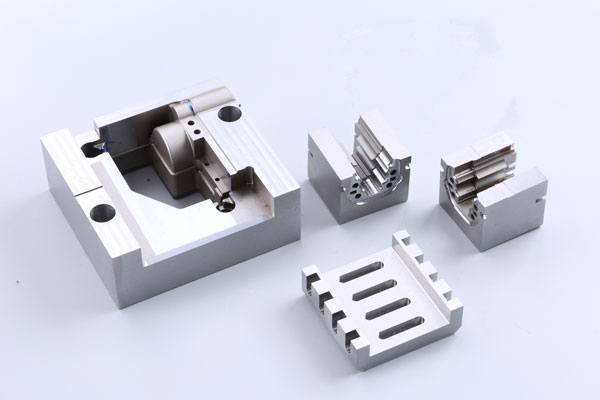
III. Pitfall Avoidance: Three Hidden Risks in Selection
- Brand Deception:
Beware of “fake tungsten carbide” (Co content <3%) prone to early cracking. Choose ISO 9001-certified suppliers with material inspection reports. - Coating Misapplication:
Avoid TiN in chlorine-rich environments (corrosion risk) and CrN in high-temp scenarios (poor thermal stability). - Maintenance Blind Spots:
Handle tungsten carbide tools gently (use dedicated jigs) to prevent hidden cracks. Clean with ultrasonic baths to avoid stress corrosion.
IV. Practical Solutions: Scenario-Based Recommendations
- 3C precision punching (e.g., mobile phone frames):
YG20C (HRA 91.5) + nano-DLC coating for 800,000-cycle lifespan and burr-free edges. - Automotive thick-plate blanking (e.g., 10mm steel):
CD-750 gradient tungsten carbide (surface HRA 90, core HRB 88) + electromagnetic-assisted punching to eliminate cracking. - Medical micro-hole punching (e.g., 0.2mm holes):
Custom YG6X pins (0.01mm edge radius) + full carbide guide bushings for burr-free results.
V. Conclusion: Equip Your Production with Science-Backed Tools
Selecting tungsten carbide punches and pins is a cross-disciplinary art merging material science, tribology, and cost engineering. By adopting a material-process-cost decision matrix, manufacturers can achieve:
✅ 40% faster production (reduced downtime)
✅ 3x longer mold lifespan (lower per-unit cost)
✅ <0.5% defect rate (ultra-precision quality)
Your Partner in Tungsten Carbide Solutions: Dongguan Yize Mould
With 15 years of expertise in hard-alloy precision machining, we offer custom design, prototyping, and post-sales support.
Contact Us: +86 13302615729 (WeChat/WhatsApp) for a free “Tungsten Carbide Punch Selection Guide” and sample testing!