In – depth Analysis of Common Problems and Causes of Tungsten Carbide
Tungsten carbide, a high – performance material made from hard compounds of refractory metals and binder metals through powder metallurgy, boasts excellent characteristics such as high hardness, wear resistance, and […]
Tungsten carbide, a high – performance material made from hard compounds of refractory metals and binder metals through powder metallurgy, boasts excellent characteristics such as high hardness, wear resistance, and corrosion resistance. It is widely used in fields such as cutting tools, molds, and wear – resistant parts. However, due to the influence of various factors during production, use, and processing, tungsten carbide often encounters some problems. Next, we will delve into these common problems and their causes.
I. Poor Thermal Stability
Tungsten carbide is prone to oxidation and corrosion at high temperatures, and its thermal stability is relatively poor, which limits its operating temperature and application environment. When exposed to high temperatures, especially above its normal operating temperature, tungsten carbide is susceptible to oxidation reactions, leading to the formation of an oxide layer on the surface, which in turn reduces its hardness and wear resistance. In addition, thermal expansion is also likely to occur in tungsten carbide at high temperatures. If the coefficient of thermal expansion does not match that of other materials, it can easily lead to cracks and fractures.
Our factory business: carbide parts, mold parts, medical injection molds, precision injection molds, teflon PFA injection molding, PFA tube fittings. email: [email protected],whatsapp:+8613302615729.
Cause Analysis
- Material Composition: Tungsten carbide is mainly composed of hard phases such as tungsten carbide (WC) and titanium carbide (TiC), as well as a binder phase such as cobalt (Co). The thermal stability of these components directly affects the thermal stability of tungsten carbide.
- Production Process: Production process parameters such as sintering temperature, sintering time, and sintering atmosphere have a significant impact on the thermal stability of tungsten carbide. If the sintering temperature is too high or the sintering time is too long, it can cause the grains of tungsten carbide to grow, thereby reducing its thermal stability.
- Operating Environment: When used in harsh environments such as high temperature, high pressure, and high speed, tungsten carbide is vulnerable to thermal stress, which can lead to problems such as oxidation, corrosion, and thermal expansion.
II. Susceptibility to Fracture
Tungsten carbide has high hardness and high brittleness, making it prone to cracks and fractures. Especially when used under high loads and high speeds, it is susceptible to fatigue damage, which can lead to fractures. In addition, the production process of tungsten carbide can also affect its fracture performance. For example, pores and inclusions in the material can all impact the fracture performance.
Cause Analysis
- Material Characteristics: Tungsten carbide itself has the characteristics of high hardness and high brittleness, which makes it prone to fracture when subjected to external impact or vibration.
- Production Process: During the production of tungsten carbide, if the pressing parameters are inappropriate, the sintering furnace parameters are not suitable, or the raw materials contain too much gas, it can lead to defects such as pores or inclusions inside or on the surface of the tungsten carbide. These defects can significantly reduce the strength and toughness of tungsten carbide.
- Operating Conditions: When using tungsten carbide under harsh conditions such as high loads and high speeds, due to its high hardness and brittleness, it is susceptible to fatigue damage and subsequent fracture. In addition, it is also prone to fracture when subjected to impact or vibration.
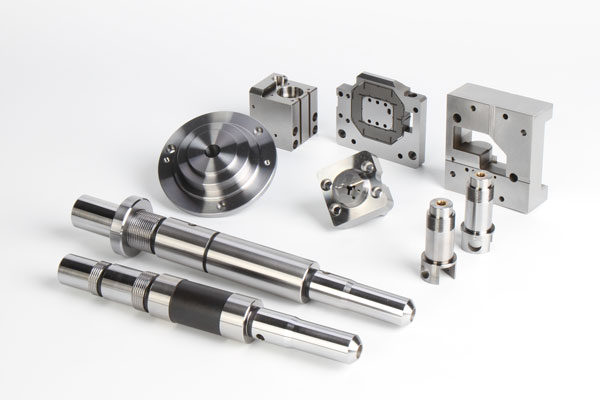
III. High Processing Difficulty
As a difficult – to – machine material, tungsten carbide presents significant processing challenges, mainly manifested in the following aspects.
- High Hardness: The hardness of tungsten carbide is much higher than that of ordinary steel. This requires the use of high-hardness cutting tools or grinding tools during processing, and also tends to generate high grinding forces and high grinding heat.
- High Brittleness: The high brittleness of tungsten carbide makes it prone to cracks and fractures during processing, which affects the processing accuracy and surface quality.
- Similar Elastic Limit and Strength: The elastic limit and strength of tungsten carbide are very close, making it difficult to control material deformation and stress distribution during processing.
Cause Analysis
- Material Characteristics: The high hardness and brittleness of tungsten carbide are the main reasons for its high processing difficulty. In addition, the poor thermal conductivity of tungsten carbide makes it difficult for the heat generated during processing to dissipate quickly, further exacerbating the processing difficulty.
- Processing Technology: Currently, the processing technology for tungsten carbide is not yet mature and perfect. Although traditional grinding processing methods can meet certain processing needs to some extent, they have problems such as low grinding efficiency and high costs. In addition, although special processing technologies such as ultrasonic and electrolytic processing can solve some of the processing problems of tungsten carbide to a certain extent, they also suffer from low processing efficiency and high costs.
IV. Conclusion
In summary, tungsten carbide often encounters problems such as poor thermal stability, susceptibility to fracture, and high processing difficulty during production, use, and processing. The causes of these problems mainly lie in factors such as material characteristics, production processes, and operating conditions. To solve these problems, we need to start from aspects such as material composition, production processes, and operating conditions, and continuously optimize and improve the production and use technologies of tungsten carbide. At the same time, we also need to strengthen research and development efforts on tungsten carbide to promote continuous innovation and development of its technology.