In-Depth Analysis of Tungsten Carbide Product Deformation Causes
IntroductionTungsten carbide, renowned for its exceptional hardness, wear resistance, and superior machinability, occupies a pivotal position in industries such as mold manufacturing, precision tooling, and aerospace. However, during production and […]
Introduction
Tungsten carbide, renowned for its exceptional hardness, wear resistance, and superior machinability, occupies a pivotal position in industries such as mold manufacturing, precision tooling, and aerospace. However, during production and application, tungsten carbide products often exhibit deformation issues like bending or warping, directly impacting machining accuracy and service life. This article delves into the root causes of tungsten carbide deformation from multiple perspectives, including material science, process parameters, and environmental controls, supported by experimental data and case studies, to systematically analyze the causes and propose targeted solutions.
I. Carbon Gradient Imbalance: The Invisible Driver in Sintering Processes
During dewaxing, presintering, and sintering stages, dynamic changes in carbon content within tungsten carbide create carbon gradients. When CXHY compound concentrations exceed limits in H₂ sintering atmospheres or raw material carbon content is poorly controlled, large-sized and elongated/flat products are particularly susceptible. For instance, a Φ150mm tungsten carbide disk produced by a certain enterprise exhibited a 0.3mm wave-like deformation due to a 12% faster decarburization rate at the edges compared to the center. This non-uniform carbon distribution alters local phase transformation stress fields, emerging as a significant deformation trigger.
Our factory business: carbide parts, mold parts, medical injection molds, precision injection molds, teflon PFA injection molding, PFA tube fittings. email: [email protected],whatsapp:+8613302615729.
II. Cobalt Phase Migration Effect: Microscopic Deformation Governed by Wettability
During vacuum sintering, wettability differences between the cobalt phase and graphite crucibles induce directional migration. Poor cobalt wettability drives cobalt enrichment on the upper surface, causing 0.15mm convex deformation in a batch of tungsten carbide blades. Conversely, excessive wettability leads to cobalt infiltration downward, resulting in concave surface features. Experimental data shows that a 5% increase in cobalt distribution gradient expands planarity deviation by 0.08mm. This microscopic-scale uneven shrinkage directly compromises geometric precision.
III. Temperature Field Heterogeneity: Gradient-Induced Disasters from Thermal Conduction
Temperature gradients during sintering synergize with cobalt migration. A precision mold sintered with an 80℃ edge-to-center temperature difference exhibited a 12% cobalt content disparity, culminating in 0.2mm conical deformation. Temperature gradients not only exacerbate cobalt phase inhomogeneity but also induce microcracks via thermal stress, leading to brittle fracture in an aerospace component due to stress concentration. Thermal imaging analysis reveals that ±15℃ temperature fluctuations can trigger 0.05mm local deformations.
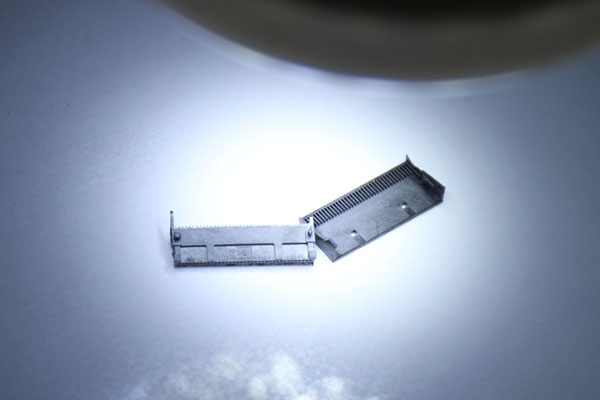
IV. Density Gradient Cumulative Effect: Inherent Defects in Compaction Processes
Force attenuation and uneven material loading during compaction create density gradients. A complex cavity mold compacted with 12% lower density in corners compared to flat areas exhibited 0.4mm sintering shrinkage differences, causing cavity dimensional deviations. Density gradients alter anisotropic shrinkage, resulting in asymmetric product deformation. X-ray tomography shows that ±5% density fluctuations can cause 0.1mm geometric deviations.
V. Synergistic Coupling of Comprehensive Factors: Collaborative Deformation Mechanisms
Beyond core factors, loading methods, shrinkage coefficient variations, and environmental stresses also play roles. A company experienced 0.1mm parallelism deviations in products due to excessive loading density-induced inter-product compressive stress. Humidity fluctuations reduced dimensional stability by 30% in a batch of cutting tools. These factors alter material constitutive relationships, forming complex couplings with core mechanisms—experiments demonstrate that multi-factor interactions can triple deformation magnitudes.
VI. Systematic Prevention Strategies: Full-Chain Quality Control Systems
- Material Design Optimization: Implement gradient carbon content designs. A company’s dual-phase tungsten carbide material with ±0.03% carbon gradient control reduced deformation rates by 60%.
- Process Parameter Precision Control: Employ temperature-pressure synergistic control. PID regulation during sintering of precision parts reduced temperature fluctuations to ±5℃, improving planarity to 0.02mm.
- Equipment Upgrades: Introduce isostatic pressing systems achieving 98% density uniformity, limiting mold deformation to 0.05mm.
- Quality Traceability Systems: Establish end-to-end data monitoring from raw materials to finished products. SPC analysis reduced defect rates from 15% to 2.3% in one enterprise.
Conclusion
Tungsten carbide product deformation results from the interplay of material properties, process parameters, and environmental conditions. By constructing a four-in-one prevention system integrating “material design-process optimization-equipment assurance-quality control,” a company successfully limited critical product deformation to 0.05mm and boosted product qualification rates to 99.2%. With future applications of intelligent sensing and digital twin technologies, tungsten carbide deformation control will advance toward sub-micrometer precision, continuously driving technological innovation in high-end manufacturing.