Revelation of the Processing Specifications of Tungsten Carbide Drawing Dies
In the grand landscape of industrial production, tungsten carbide drawing dies shine like a bright star, occupying a pivotal position. They are like a highly skilled craftsman, precisely shaping various […]
In the grand landscape of industrial production, tungsten carbide drawing dies shine like a bright star, occupying a pivotal position. They are like a highly skilled craftsman, precisely shaping various products. The processing specifications of these dies directly determine the quality of the products and the efficiency of production. Next, let’s delve into the mysteries of the processing specifications of tungsten carbide drawing dies to better master this key tool and inject powerful momentum into industrial production.
I. Die Size and Position of Locking Screws: Precise Adaptation, Solid Foundation
In the processing journey of tungsten carbide drawing dies, the selection of die size is of utmost importance. An appropriate die size is like a tailor-made suit for the product, which must be larger than the working area to ensure that the die can operate freely during the working process. To achieve versatility and convenience, standard template sizes are usually chosen. This approach not only greatly facilitates the manufacturing and maintenance of the dies but also enables them to fit together seamlessly, improving production efficiency and making the entire production process smoother and more efficient.
Our factory business: carbide parts, mold parts, medical injection molds, precision injection molds, teflon PFA injection molding, PFA tube fittings. email: [email protected],whatsapp:+8613302615729.
Meanwhile, the configuration of the positions of locking screws is like building a sturdy framework for the die, which is a key link in die design. The positions of locking screws are not randomly determined but are closely related to the type of die and the template size. Take single-stage dies as an example. The locking screws usually stand like loyal guards at the four corners. This clever configuration can widely adapt to the needs of various working areas, providing a solid guarantee for the stable operation of the die. For long dies or progressive dies, due to their more complex structures, locking screws also need to be reasonably configured in the middle positions in addition to the four corners. This is like setting support columns at key nodes of a bridge, ensuring that the die maintains stability and precision in complex working environments and laying a solid foundation for producing high-quality products.
II. Template Thickness: Weighing Pros and Cons, Scientific Decision-making
The thickness of the template is like the backbone of the tungsten carbide drawing die and is one of the key factors in its processing specifications. It directly affects the strength, rigidity, and service life of the die, just as the depth of a building’s foundation determines the stability of the entire building. The selection of template thickness is not a simple task but requires a comprehensive consideration of multiple factors, such as the structure of the die, the type of stamping process, the processing force, and the processing accuracy. These factors are intertwined like a complex network, requiring engineers to make precise trade-offs based on their rich experience and professional knowledge.
Theoretically, determining the thickness of the die through precise calculations is the ideal choice. However, in actual production, due to the complexity and uncertainty of various factors, it is often difficult to achieve. Therefore, in practical operations, we rely more on experience to select the appropriate thickness. To facilitate procurement and inventory management and improve production efficiency, the number of template thickness types used in design should be minimized as much as possible, and standardization should be carried out according to the height of the die and the clamping height. This is like unifying currency specifications, facilitating circulation and use, and making the entire production process more orderly and efficient.
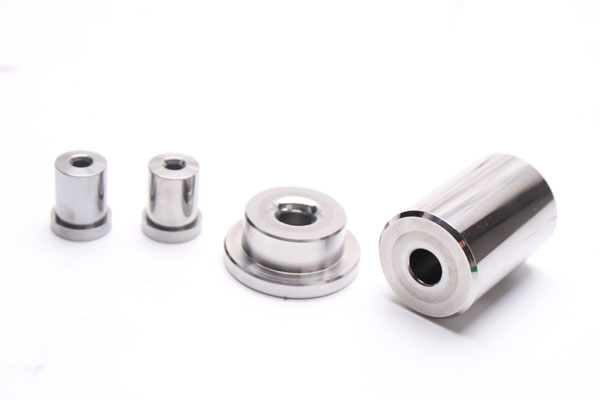
III. Material Selection and Treatment: Careful Selection, Enhanced Performance
Tungsten carbide, as the main material for drawing dies, stands out as the first choice for die manufacturing with its excellent characteristics of high hardness and good wear resistance. However, tungsten carbide materials also face challenges during the processing. The influence of temperature on their dimensions is an issue that cannot be ignored. Generally speaking, tungsten carbide begins to show dimensional changes in the temperature range of 120℃ – 200℃, mainly due to the material’s coefficient of thermal expansion. This is similar to the principle of thermal expansion and contraction, where temperature changes cause subtle changes in the dimensions of the material, thus affecting the precision of the die. Therefore, during the processing, the temperature must be strictly controlled, just as a chef controls the heat precisely, to avoid adverse effects on the precision of the die due to dimensional changes.
In addition, to improve the performance and service life of the die, appropriate heat treatment and other surface treatments can be carried out on the tungsten carbide material. These treatment measures are like putting on a sturdy armor for the die, further enhancing the hardness and wear resistance of the material. Heat treatment can change the internal structure of the material and improve its comprehensive performance; surface treatment can form a protective film on the surface of the die, effectively preventing corrosion and oxidation and extending the service life of the die. Through these treatment measures, the die can maintain excellent performance in harsh working environments and provide a strong guarantee for producing high-quality products.
IV. Processing Precision and Surface Treatment: Striving for Perfection, Pursuing Excellence
The processing precision of tungsten carbide drawing dies is an important indicator for measuring die quality and directly affects the quality of products and production efficiency. During the processing, each parameter must be strictly controlled, just as a sculptor carefully carves an artwork, ensuring that the precision of the die meets the requirements. Every dimension and every angle need to be accurate to the micrometer level, leaving no room for error. Only by achieving high-precision processing requirements can products with precise dimensions and stable quality be produced to meet the market’s demand for high-quality products.
Meanwhile, to improve the service life and performance of the die, surface treatments such as chrome plating and nitriding can also be carried out. These treatment measures are like giving the die a makeover and strengthening it, not only improving the hardness and wear resistance of the die but also effectively preventing corrosion and oxidation. Chrome plating can form a smooth and hard chromium layer on the surface of the die, improving its wear resistance and corrosion resistance; nitriding can form a high-hardness nitride layer on the surface of the die, enhancing its wear resistance and fatigue resistance. Through these surface treatment measures, the die can maintain good performance during long-term use, saving costs for enterprises and improving production efficiency.
V. Summary and Prospects: Keeping Up with Trends, Innovative Development
In summary, the processing specifications of tungsten carbide drawing dies involve multiple aspects, including size, position of locking screws, template thickness, material selection, and processing precision. These factors are interrelated and influence each other, jointly determining the performance and service life of the die. To ensure that the die can perform at its best, we need to comprehensively consider these factors and carry out reasonable design and optimization. Just as an excellent conductor can skillfully coordinate the performance of various musical instruments to create beautiful music.
With the continuous progress of science and technology and the emergence of new materials and new processes, the processing specifications of tungsten carbide drawing dies in the future will continue to be optimized and improved. New materials may have higher hardness, better wear resistance, and a lower coefficient of thermal expansion, providing more choices for die manufacturing; new processes may be more efficient and precise, enabling the production of dies with higher quality and more stable performance. Therefore, it is recommended that relevant practitioners closely follow industry trends and technological development trends, actively participate in various training and academic exchange activities, and continuously learn and master the latest processing technologies and specifications. Only in this way can we remain invincible in the fierce market competition and make greater contributions to the development of industrial production.
Let’s work together to continuously explore new areas of the processing specifications of tungsten carbide drawing dies and contribute to the brilliant future of industrial production!
Related Posts
- How to use tungsten carbide to process efficiency and extend tool life
- Key Points to Note in the Cracking Process of Tungsten Carbide Tool Grinding
- Maintenance Secrets of Tungsten Carbide Blades: A Comprehensive Guide to Prolonging Lifespan and Enhancing Performance
- Tungsten Carbide Dies: The “Hard – Core Backbone” of Modern Industry