Tungsten Carbide Dies: The Evolutionary Path in the Industrial Arena
Tungsten carbide holds a pivotal position in the die industry, renowned for its exceptional hardness, wear resistance, and corrosion resistance. With the continuous advancement of modern industry, the application scope […]
Tungsten carbide holds a pivotal position in the die industry, renowned for its exceptional hardness, wear resistance, and corrosion resistance. With the continuous advancement of modern industry, the application scope of tungsten carbide dies has expanded significantly, playing an irreplaceable role in fields such as machinery manufacturing, the electronics industry, and automobile manufacturing. This article delves into the development trajectory, technical characteristics, current application status, and future trends of tungsten carbide dies, aiming to provide valuable references and insights for relevant practitioners.
I. Development History of Tungsten Carbide Dies
As a novel material, tungsten carbide has garnered widespread attention since its inception in the early 20th century due to its unique physical and chemical properties. Tungsten carbide is primarily manufactured by compressing and sintering refractory metal carbides (such as tungsten carbide, WC) and metal binders (such as cobalt, Co) through the powder metallurgy method. Its high hardness, strength, wear resistance, and high elastic modulus make it an ideal material for die manufacturing.
Our factory business: carbide parts, mold parts, medical injection molds, precision injection molds, teflon PFA injection molding, PFA tube fittings. email: [email protected],whatsapp:+8613302615729.
In the early days, tungsten carbide dies were mainly used for cutting tools and wear-resistant parts. With technological progress and material improvements, their application areas gradually broadened. Especially under the demand for high-precision and high-efficiency modern processing, the advantages of tungsten carbide dies became increasingly prominent. They gradually replaced some traditional die materials, becoming a crucial pillar of the die industry.
II. Technical Characteristics of Tungsten Carbide Dies
- High Hardness and Wear Resistance: The hardness of tungsten carbide far exceeds that of ordinary steel. This characteristic enables tungsten carbide dies to maintain their sharpness and precision for an extended period during use, significantly prolonging their service life. Imagine in long-term, high-intensity processing tasks, ordinary steel dies may wear out quickly, while tungsten carbide dies remain as sharp as ever, greatly saving costs and time for enterprises.
- Good Thermal Stability: Tungsten carbide can retain high hardness and strength even at high temperatures. This makes it perform exceptionally well in high-temperature processing environments such as high-speed cutting and heavy-load processing. Like a warrior tempered in the flames, it fearlessly and efficiently completes various tasks, providing a solid guarantee for improving production efficiency.
- Excellent Corrosion Resistance: Tungsten carbide exhibits strong resistance to many chemical media. In harsh environments like the chemical and marine industries, where dies often have to withstand the attacks of various corrosive substances, tungsten carbide dies act as a knight in armor, protecting the normal operation of equipment parts and safeguarding production in special industries.
- High-Precision Machining Capability: Tungsten carbide dies can achieve high-precision machining, meeting the stringent requirements of modern industry for product quality and accuracy. In an era where extreme quality is pursued, every minor dimensional deviation may affect the performance and reliability of products. Tungsten carbide dies, with their excellent machining capabilities, can precisely shape various complex-shaped parts, laying a solid foundation for high-quality products.
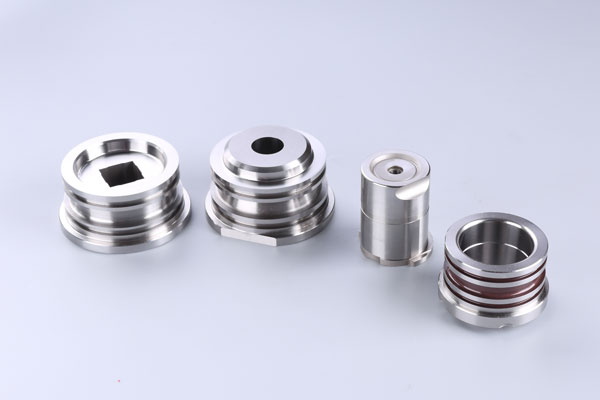
III. Current Application Status of Tungsten Carbide Dies
- Machinery Manufacturing Industry: In the vast field of machinery manufacturing, tungsten carbide dies are like precise tools, widely used in cutting tools, stamping dies, extrusion dies, etc. In cutting operations, their high hardness and wear resistance enable cutting tools to stay sharp for a long time, acting as sharp swords that cut through iron like mud, greatly improving processing efficiency. In stamping and extrusion processes, they can withstand enormous pressures and frictional forces, ensuring the quality and precision of products, and injecting strong impetus into the vigorous development of the machinery manufacturing industry.
- Electronics Industry: With the rapid development of electronic products towards miniaturization and precision, the application of tungsten carbide dies in the electronics industry has become increasingly widespread. They serve as capable assistants in manufacturing micro-parts, integrated circuit packaging dies, etc. Like skilled miniature sculptors, they create exquisite products in tiny spaces, providing powerful support for the continuous innovation and upgrading of electronic products.
- Automobile Manufacturing Industry: The automobile manufacturing industry has extremely stringent requirements for the precision and durability of dies. Tungsten carbide dies, with their outstanding performance and stability, have become the cornerstone of the manufacturing process for key components such as automobile engines and gearboxes. They ensure the high precision and quality of these core components, providing a solid guarantee for the safe driving and excellent performance of automobiles, and driving the automobile industry to new heights.
IV. Future Trends of Tungsten Carbide Dies
- Material Innovation: With the continuous progress of materials science, a wave of material innovation is expected in the future for tungsten carbide dies. By adopting advanced modification methods such as adding rare earth elements, the hardness and wear resistance of tungsten carbide can be further enhanced. It is like injecting new vitality into the dies, enabling them to handle more complex and harsh processing environments with ease and create more brilliant achievements.
- Intelligent Manufacturing: In the era of the booming development of intelligent manufacturing technology, the manufacturing process of tungsten carbide dies will accelerate its transformation towards automation and intelligence. Advanced numerical control technology, sensor technology, and artificial intelligence technology will be deeply integrated into the manufacturing process, achieving precise control and optimization of die manufacturing. It is like a craftsman with a wise brain who can flexibly adjust manufacturing parameters according to different needs and working conditions to create more perfect and efficient die products.
- Green and Environmentally Friendly: Against the backdrop of the global advocacy for green and environmentally friendly practices, the manufacturing and use of tungsten carbide dies will place greater emphasis on environmental performance. Adopting environmentally friendly materials and processes to reduce pollution and waste emissions during the production process will become an inevitable trend in the industry. This is not only a responsibility towards the Earth’s home but also the only way for enterprises to achieve sustainable development, allowing tungsten carbide dies to coexist harmoniously with nature while driving industrial progress.
- Customized Services: With the increasing diversification of market demands, customized services for tungsten carbide dies will become a popular trend in the future. Manufacturers will tailor-make die design and manufacturing solutions according to the personalized needs of customers, like creating exclusive “fashion gowns” for each customer, meeting the specific requirements of different industries and products, and helping enterprises gain an edge in the fierce market competition.
V. Conclusion
Tungsten carbide dies, with their outstanding performance and wide application areas, have already become an indispensable support for modern industry. In the era of rapid technological progress and industrial development, the tungsten carbide die industry faces both unprecedented opportunities and new challenges. Only by continuously innovating and improving technological levels can it remain invincible in the fierce market competition and usher in broader development space and brighter market prospects. Let us look forward to the tungsten carbide die industry writing even more magnificent chapters in the future!