Tungsten Carbide Dies: The “Industrial Titan” Reshaping Manufacturing Efficiency
In the arena of precision manufacturing, dies serve as the “teeth” of industrial machinery, while tungsten carbide dies (cemented carbide dies) stand out as the “titanium-alloy-grade fangs.” With their “indestructible hardness” and […]
In the arena of precision manufacturing, dies serve as the “teeth” of industrial machinery, while tungsten carbide dies (cemented carbide dies) stand out as the “titanium-alloy-grade fangs.” With their “indestructible hardness” and “steel-like toughness,” these dies are sparking a “material revolution” in high-precision fields such as electronics, medical devices, and automotive engineering. This article delves into the core advantages, manufacturing innovations, and industry applications of tungsten carbide dies, revealing how they are redefining industrial manufacturing standards through hardcore capabilities.
I. Performance DNA: Four Core Strengths Crafting an “Industrial Invincible Shield”
The exceptional performance of tungsten carbide dies stems from their “ultra-hardcore” material formulation (tungsten carbide grains + cobalt binder), granting them four “superpowers”:
Our factory business: carbide parts, mold parts, medical injection molds, precision injection molds, teflon PFA injection molding, PFA tube fittings. email: [email protected],whatsapp:+8613302615729.
- “Unbreakable” Wear Resistance
- Microscopic Battle: Tungsten carbide grains reach nanoscale levels, with hardness up to HRA90-94 (approaching diamond). In high-speed stamping (e.g., thousands of strokes per minute), cavity wear is reduced by 90% compared to Cr12MoV steel.
- Long-Term Protection: A smartphone mid-frame stamping die using tungsten carbide increased its lifespan from 50,000 to 800,000 cycles, slashing per-unit die cost allocation by 87%.
- “Impact-Resistant” Flexible Strength
- Rigid Yet Flexible: The cobalt binder phase provides 10-15% fracture toughness (KIC value). In automotive panel drawing dies, it withstands 1,500 MPa-level impact loads without brittle fracture, reducing die breakage rates by 60% compared to conventional dies.
- Energy Absorption: Achieves a synergistic effect of “hard-phase load-bearing + binder-phase cushioning” under dynamic loads through microstructure optimization.
- “Thermal Shock-Proof” Temperature Control Master
- Thermal Fatigue Resistance: Endures 20,000 cycles of rapid cooling from 300°C to -20°C (e.g., in die-casting dies), 5 times longer than H13 steel.
- Microscopic Stability: Suppresses grain boundary oxidation and phase transformation via rare earth element doping, ensuring hardness drop <5% at high temperatures.
- “Acid-Alkali-Proof” Chemical Shield
- Corrosion Resistance Code: Forms a dense tungsten trioxide (WO₃) protective film, with a corrosion rate of just 0.001 mm/year in PVC processing (containing chloride corrosion), tripling die lifespan.
- Scenario Breakthrough: Withstands HF acid environments in semiconductor packaging dies, meeting stringent requirements for wafer-level packaging.
II. Manufacturing Alchemy: From “Costly Material” to “Mass-Production Powerhouse”
Despite their high cost, tungsten carbide dies achieve a “high-value, low-cost” balance through material innovation + precision manufacturing:
- “Shape-Shifting” Forging Revolution
- Low-Temperature Forging: Achieves superplastic deformation at 1,100-1,200°C (200°C lower than conventional steel), reducing energy consumption by 30% while avoiding abnormal grain growth.
- Near-Net-Shape Forming: Attains 95% near-net-shape accuracy via powder metallurgy + isostatic pressing, cutting finishing allowance by 40%.
- “Cutting Through Steel” Machining Breakthroughs
- Tool Revolution: PCBN (cubic boron nitride) tools + high-speed cutting (surface speed >200 m/min) boost efficiency 5x over carbide tools, achieving surface roughness Ra≤0.2 μm.
- Smart Programming: Optimizes cutting paths via CAE simulation to prevent tool chipping, slashing single-part machining time by 60%.
- “Quenching Mysticism” Heat Treatment Breakthroughs
- Vacuum Quenching: Achieves 1,220°C quenching + 560°C triple tempering in 10⁻³ Pa vacuum, ensuring ±1 HRA hardness uniformity and <0.02 mm distortion.
- Cryogenic Treatment: Eliminates retained austenite via -196°C liquid nitrogen quenching, raising hardness by 2-3 HRA and wear resistance by 15%.
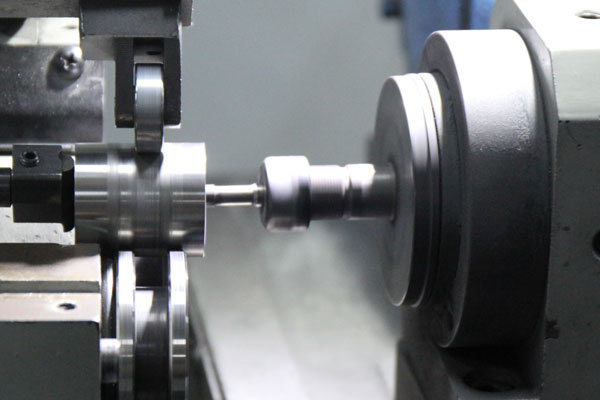
III. Industry Application Atlas: Tungsten Carbide Dies’ “Versatile Battlefields”
From microscopic components to macroscopic equipment, tungsten carbide dies are penetrating industries with “customized solutions”:
- Electronics Arena: “Elite Weapons” in Millimeter-Scale Warfare
- Foldable Screen Hinges: A manufacturer uses tungsten carbide progressive dies to achieve 0.01 mm-level synchronous bending precision, with folding lifespan exceeding 500,000 cycles.
- Mini LED Chips: Through micro-hole array dies (50 μm aperture), 2,000+ pins are stamped in a single cycle, with yield >99.5%.
- Medical Sanctum: “Life Sculptors” with Nanoscale Precision
- Cardiovascular Stents: Tungsten carbide micro-electrode dies process nickel-titanium alloy stents with 0.1 mm wire diameter, 0.02 mm wall thickness, and surface roughness Ra≤0.1 μm.
- Artificial Joints: Achieves a perfect balance of porous structure (60% porosity) and biomechanical properties via powder metallurgy + tungsten carbide die pressing.
- Automotive Empire: “Steel Tailors” Under Mega-Tonnage Pressure
- Integrated Die-Casting Dies: Withstands 150 MPa pressure in 9,000-ton die-casting machines, forming Tesla Model Y rear floors with 30% weight reduction and 40% cost savings.
- Hydrogen Fuel Cell Bipolar Plates: Through micro-channel dies (0.3 mm channel width, 0.2 mm depth), single plate forming time is <8 seconds, meeting million-unit annual production demands.
- Cross-Industry Pioneers: From Cutting Tools to Aerospace Giants
- Ultra-Hard Cutters: Tungsten carbide substrates + PCD/CBN coatings triple titanium alloy machining efficiency, with tool lifespan reaching 2,000 meters.
- Aerospace Bearings: Uses tungsten carbide cage dies to achieve bearing speeds exceeding 100,000 RPM under -180°C to 350°C extreme temperatures.
IV. Future Evolution: The “Three-Body Revolution” of Tungsten Carbide Dies
Facing Industry 4.0 trends, tungsten carbide dies are evolving across materials, processes, and ecosystems:
- Material Revolution: From “Single Hardness” to “Smart Hardness”
- Gradient Functional Materials: Surface ultra-hard layer (WC-Co) + core toughening layer (WC-Ni) balance wear resistance and impact resistance.
- Self-Healing Coatings: Nano-ceramic/metal-organic framework (MOF) composite coatings enable microscopic crack self-repair.
- Process Revolution: From “Subtractive Manufacturing” to “Additive Empowerment”
- 3D-Printed Dies: Laser selective melting (SLM) technology forms complex flow channel dies, cutting development cycles by 70%.
- Digital Twins: Predicts die lifespan via AI, enabling “on-demand maintenance” over “periodic replacement.”
- Ecosystem Revolution: From “Point Breakthroughs” to “Full-Chain Enablement”
- Circular Economy: Boosts tungsten carbide scrap recycling rate to 98%, with recycled material performance matching virgin material.
- Cloud Manufacturing Platform: Integrates design, processing, and inspection resources for “one-click” die solutions.
Conclusion: The Flexible Future of Hardcore Materials
From “industrial teeth” to “intelligent cores,” the evolution of tungsten carbide dies mirrors a micro-industrial revolution. When 3D printing meets ultra-hard materials, and digital twins empower traditional processes, these dies are reshaping manufacturing logic with “hardcore strength + flexible wisdom.” In the future, they will transcend being mere tools to become “super interfaces” connecting the physical and digital worlds, continuously unlocking “hardcore dividends” in strategic fields like micro-nano manufacturing, new energy, and aerospace.