Tungsten Carbide Thermal Drill
1. Introduction: The “Hardcore Drill General” in the Tide of Industrial Evolution In today’s era of rapid technological advancement in industry, the pursuit of tool performance in manufacturing has reached […]
1. Introduction: The “Hardcore Drill General” in the Tide of Industrial Evolution
In today’s era of rapid technological advancement in industry, the pursuit of tool performance in manufacturing has reached unprecedented heights. Tungsten carbide thermal drills, a “cutting-edge” technology in the realm of cemented carbides, are quietly reshaping the landscape of metal processing with their revolutionary processing logic and remarkable adaptability. From automotive bodies to aerospace components, from precision instruments to household items, they have become indispensable “all-rounders” in modern industry with their “hardcore” capabilities. This article will delve into the performance secrets of tungsten carbide thermal drills and unveil how they “shine” in diverse scenarios.
2. Performance Decoding: The “Hexagonal Warrior” Genes of Tungsten Carbide Thermal Drills
2.1 Hardcore Material: The “Diamond-Like” Wear-Resistant Drill
Tungsten carbide thermal drills are forged from tungsten carbide cemented carbide, boasting a hardness comparable to that of diamonds. They maintain their sharpness even under extreme conditions of high temperature and high-speed rotation. Whether tackling the “toughness” of stainless steel or the “aloofness” of titanium alloys, they can effortlessly handle these challenges with their long service life and stable performance, earning them the title of “endurance warriors” in the metal processing world.
Our factory business: carbide parts, mold parts, medical injection molds, precision injection molds, teflon PFA injection molding, PFA tube fittings. email: [email protected],whatsapp:+8613302615729.
2.2 Efficiency Revolution: The Production “Accelerator” with a 2-Second Breakthrough
Traditional drilling processes involve multiple steps, whereas tungsten carbide thermal drills can complete an entire processing cycle in just 2–6 seconds. This “lightning-fast” efficiency is a game-changer for large-scale component production, especially in high-cadence fields like automotive manufacturing, serving as a “secret weapon” for boosting productivity.
2.3 Precision Aesthetics: The “Detail-Oriented” Craftsmanship at the Millimeter Level
Thermal drills not only drill holes with precision but also form annular bosses at the hole openings, directly replacing the cumbersome process of traditional drilling followed by riveting. This design not only enhances connection strength but also gives products a smoother appearance, embodying a perfect fusion of industrial design and functional aesthetics.
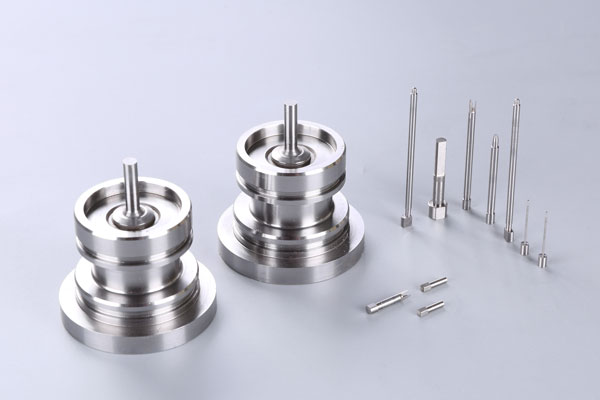
2.4 Green Manufacturing: The “Eco-Pioneer” of Chip-Free Processing
Traditional drilling generates a large amount of chips, while thermal drills achieve nearly “chip-free” production through their “melting-extrusion” forming technology. A dust-free and pollution-free processing environment not only complies with environmental regulations but also reduces cleaning costs, making them a “standard configuration” for modern green factories.
2.5 Universal Adaptability: The “Master Key” for Metal Processing
From mild steel to titanium alloys, from thin sheets to thick tubes, tungsten carbide thermal drills can overcome almost all metal processing challenges. This “cross-material, cross-thickness” adaptability makes them “all-round players” in manufacturing capable of taking on a multitude of tasks.
3. Application Landscape: A Cross-Boundary Journey from Land to Space
3.1 Automotive Industry: A Dual Evolution of Efficiency and Aesthetics
In automotive manufacturing, thermal drills directly replace traditional drilling-and-riveting processes, boosting the processing efficiency of body panels and tubular components by over 50%. What’s more, their chip-free processing characteristics leave the body surface smoother, steering automotive design towards a “seamless aesthetic.”
3.2 Bicycle Industry: The “Golden Balance” Between Lightweight and Strength
The connection of carbon fiber frames with aluminum alloy accessories demands extreme precision. Thermal drills create connection holes with micron-level precision while enhancing structural strength through annular bosses, finding the perfect fulcrum between “weight reduction” and “compression resistance” for bicycles.
3.3 Stainless Steel Furniture: A “Win-Win” of Texture and Efficiency
Behind the minimalist style of stainless steel furniture lies the “carving” of metal sheets by thermal drills. From the legs of dining tables and chairs to the connecting pieces of cabinets, they ensure surface smoothness through chip-free processing and improve assembly efficiency with precise hole positions, making industrial design both artistic and practical.
3.4 Aerospace: The “Performance Leader” in Extreme Environments
In the processing of aircraft engine blades or aerospace structural components, thermal drills face extreme tests of ultra-high temperature and high strength. Their tungsten carbide material and precision forming technology ensure processing within micron-level tolerances, providing reliable guarantees for “national heavyweights.”
3.5 Cross-Boundary King: Unlimited Possibilities from the Kitchen to Space
From the rapid drilling of kitchen sinks to the seamless connection of air conditioning ducts; from the lightweight design of fitness equipment to the precision assembly of medical devices—thermal drills’ application scenarios cover almost all metal processing fields, becoming a “universal interface” for industrial innovation.
4. Future Outlook: The “Intelligent Drill General” in the Era of Industry 4.0
As the wave of intelligent manufacturing sweeps across the industry, tungsten carbide thermal drills are deeply integrating with CNC machine tools and industrial robots to achieve real-time optimization and adaptive adjustment of processing parameters. In the future, they may be equipped with AI vision systems to automatically identify materials and thicknesses, or through nano-coating technology to further enhance wear resistance and cutting efficiency. On the track of Industry 4.0, this “hardcore drill general” is continuously expanding the boundaries of metal processing with an innovative stance.
Conclusion
Tungsten carbide thermal drills are not merely tools but the crystallization of industrial wisdom. With their “hardcore” performance as the foundation and “cross-boundary” applications as wings, they are etching brilliant trajectories in the sky of manufacturing. As technology continues to iterate and upgrade, this “drill general” will undoubtedly write more industrial legends, creating a more efficient, environmentally friendly, and intelligent production future for humanity.