Unlocking the Secrets of Tungsten Carbide Grinding
In the vast landscape of industrial production, tungsten carbide, also known as cemented carbide, stands out as a shining star. Boasting exceptional hardness, remarkable wear resistance, and outstanding high-temperature performance, […]
In the vast landscape of industrial production, tungsten carbide, also known as cemented carbide, stands out as a shining star. Boasting exceptional hardness, remarkable wear resistance, and outstanding high-temperature performance, it plays an indispensable role across various industries. Whether in cutting tools, mold manufacturing, or the production of high-end components for aerospace and automotive applications, tungsten carbide is an irreplaceable force.
However, every coin has two sides. The very high hardness of tungsten carbide, while conferring its superior properties, also significantly increases the difficulty of machining, particularly in the grinding process. Today, let’s delve deep into the grinding technology of tungsten carbide products, unraveling its unique characteristics, process flows, common issues, and corresponding solutions, aiming to provide valuable insights for practitioners in related fields.
Our factory business: carbide parts, mold parts, medical injection molds, precision injection molds, teflon PFA injection molding, PFA tube fittings. email: [email protected],whatsapp:+8613302615729.
I. Unique Challenges in Tungsten Carbide Grinding
Tungsten carbide grinding presents several distinct challenges, akin to a series of “shackles” that constantly test the skills and expertise of machinists.
1. Hardness Beyond Compare
Tungsten carbide’s hardness far surpasses that of ordinary steel, placing it at the pinnacle of the hardness hierarchy. This characteristic makes the selection and use of grinding wheels in the grinding process a critical consideration. Ordinary grinding wheels are like eggshells cracking against a rock when faced with tungsten carbide, wearing out rapidly and compromising both processing accuracy and efficiency.
2. Wear-Resistant “Armor”
The remarkable wear resistance of tungsten carbide is a double-edged sword. While it enables the material to withstand harsh conditions, it also poses difficulties for grinding. The low material removal rate means more time and effort are required, and the demands for processing precision are even stricter. A slight misstep could lead to all previous efforts going to waste.
3. Thermal Conductivity “Shortcoming”
Tungsten carbide has a low thermal conductivity, akin to donning an “insulating coat” for the workpiece. Heat generated during grinding is difficult to dissipate, causing the workpiece surface temperature to rise rapidly. This not only affects the processing quality, leading to surface defects, but also shortens the service life of the grinding wheel, increasing production costs.
4. Machining “Perilous Summit”
Taking all these characteristics into account, the grinding of tungsten carbide is undoubtedly a perilous summit to climb. It places extremely high demands on equipment, grinding wheels, coolants, and other factors. Every link in the process requires meticulous attention to detail; otherwise, machining difficulties are bound to arise.
II. Precision Navigation: The Process Flow of Tungsten Carbide Grinding
Facing the numerous challenges in tungsten carbide grinding, a scientific and rational process flow serves as our “navigation map,” guiding us smoothly towards success.
1. Selecting the Right “General” – Grinding Wheel Selection
In response to the high hardness of tungsten carbide, selecting the grinding wheel is akin to choosing capable generals for a battle. Grinding wheels with moderate hardness and good wear resistance are the top choices. Materials such as corundum and silicon carbide are suitable options. Additionally, the grit size and binder of the grinding wheel should be adjusted flexibly according to specific circumstances to ensure optimal performance during grinding.
2. Setting Up “Camp” for the Workpiece – Workpiece Clamping
The stability of the workpiece during the grinding process is of utmost importance, much like soldiers needing a firm foothold on the battlefield. Appropriate fixtures serve as the “camp” for the workpiece, securing it firmly on the grinding machine. Meanwhile, the relative position between the workpiece and the grinding wheel should be precisely adjusted to lay a solid foundation for high-precision machining.
3. Tuning the “Strings” – Parameter Setting
Grinding parameters are like the strings of a musical instrument, requiring careful adjustment to produce a harmonious melody. Parameters such as grinding depth, feed rate, and grinding wheel speed must be comprehensively considered in terms of processing efficiency, quality, and grinding wheel lifespan. Generally, the grinding depth of tungsten carbide should be appropriately reduced, and the feed rate should not be too fast to prevent excessive grinding wheel wear and workpiece surface “burns.”
4. Escorting with “Coolant” – Coolant Application
Due to the poor thermal conductivity of tungsten carbide, coolant acts as the workpiece’s “guardian angel,” promptly reducing its surface temperature, minimizing grinding wheel wear, and enhancing processing quality. Water-soluble cutting fluids and oil-based cutting fluids are commonly used coolants, providing protection throughout the grinding process.
5. Keeping a “Lookout” During the Process – In-Process Monitoring
During the grinding process, we must remain vigilant like sentinels on a lookout tower, closely monitoring the grinding wheel’s wear, the workpiece’s processing quality, and temperature changes. Once any issues are detected, grinding parameters should be promptly adjusted or the grinding wheel replaced to ensure the smooth progress of the process.
6. Post-Processing “Mop-Up” – Post-Grinding Handling
After grinding is completed, subsequent handling work should not be overlooked. Cleaning, inspection, and packaging are like tidying up the battlefield, summarizing the results after a battle. During cleaning, cutting fluids and metal chips must be thoroughly removed to prevent any impact on the workpiece’s performance. Inspection should be rigorous to ensure the workpiece’s quality meets requirements. Packaging should be meticulous to protect the workpiece from damage during transportation and storage.
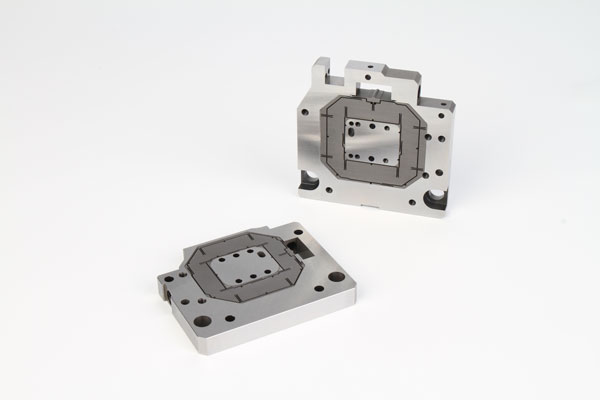
III. Breaking the Ice: Common Issues and Solutions
In the journey of tungsten carbide grinding, we are bound to encounter some “hidden reefs,” but with the right “ice-breaking techniques,” we can turn dangers into opportunities.
1. Grinding Wheel “Breakage” – Rapid Wheel Wear
Rapid grinding wheel wear is like a soldier’s weapon breaking prematurely, severely affecting the processing schedule. This may be caused by insufficient grinding wheel hardness or improper grit size selection. In such cases, we should promptly replace the grinding wheel with one of moderate hardness and suitable grit size and adjust the grinding parameters to reduce the wear rate of the grinding wheel, allowing it to regain its “sharpness.”
2. Workpiece “Scalding” – Surface Burns
Surface burns on the workpiece are like skin scalding, leaving unsightly scars that affect its performance. This is usually caused by insufficient coolant or improper setting of grinding parameters. We should increase the coolant flow rate to “cool down” the workpiece and appropriately adjust parameters such as grinding depth, feed rate, and grinding wheel speed to ensure the workpiece completes the grinding process in a comfortable “environment.”
3. Precision “Off Target” – Substandard Machining Accuracy
Substandard machining accuracy is like an arrow missing the target, nullifying previous efforts. This may be caused by unstable workpiece clamping, severe grinding wheel wear, or unreasonable setting of grinding parameters. We should check the stability of the fixture to create a solid “position” for the workpiece, promptly replace worn grinding wheels to restore their “combat effectiveness,” and optimize grinding parameters to bring the machining accuracy back on track.
IV. A New Blueprint for the Future: Summary and Outlook
The grinding of tungsten carbide materials is undoubtedly a technically challenging process that requires comprehensive consideration of multiple factors, including material characteristics, equipment performance, grinding wheel selection, and grinding parameters. It is like painting a complex picture, with every stroke needing to be precise.
Through a reasonable process flow and strict in-process monitoring, we can ensure the processing quality and efficiency of tungsten carbide workpieces, allowing tungsten carbide to unleash its greater value in industrial production. Looking ahead, with the continuous advancement of technology and the development of new grinding technologies, the grinding of tungsten carbide materials will usher in an era of greater efficiency, precision, and reliability. We have every reason to believe that in the near future, tungsten carbide materials will shine even more brightly on the industrial stage, providing a steady stream of momentum for the development of industrial production.