In-Depth Analysis: Tungsten Carbide Parts – The Hardy Pillar of the Industrial Sector
When it comes to Tungsten Carbide materials, many in the industrial machinery sector, especially those who frequently work with them, are well acquainted with their unique attributes. Tungsten Carbide parts […]
When it comes to Tungsten Carbide materials, many in the industrial machinery sector, especially those who frequently work with them, are well acquainted with their unique attributes. Tungsten Carbide parts stand out among various materials due to their exceptional hardness, outstanding wear resistance, good strength and toughness, excellent heat and corrosion resistance. Notably, even at temperatures up to 500℃, their high hardness and wear resistance remain steadfast, and they still exhibit considerable hardness at 1000℃, demonstrating remarkable thermal stability.
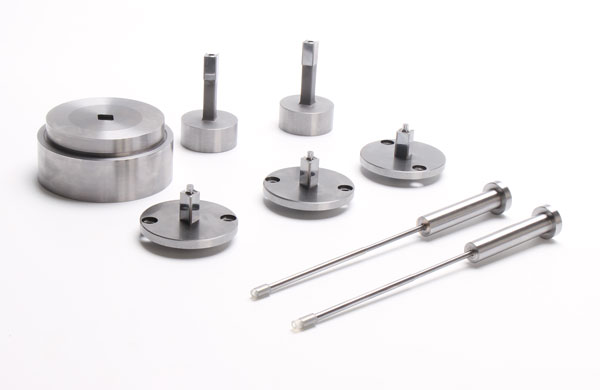
Tungsten Carbide components, also known as cemented carbide parts, are meticulously crafted composites consisting of at least one metal carbide. Tungsten carbide, cobalt carbide, niobium carbide, titanium carbide, and tantalum carbide are common constituents of Tungsten Carbide. The grain size of these carbide components (or phases) typically ranges from 0.2 to 10 micrometers, with carbide grains bonded together using a metal binder. The binder is usually metallic cobalt (Co), but for specific applications, nickel (Ni), iron (Fe), or other metals and alloys may also be used. A specific combination of carbide and binder phase components is referred to as a “grade”.
Our factory business: carbide parts, mold parts, medical injection molds, precision injection molds, teflon PFA injection molding, PFA tube fittings. email: [email protected],whatsapp:+8613302615729.
The classification of Tungsten Carbide components follows ISO international standards, which are primarily based on the material category of the workpiece, taking into account the strength and corrosion resistance of the binder phase, ensuring a scientific and practical classification system.
Delving into the matrix structure of Tungsten Carbide components, it comprises two core components: the hardening phase and the binder metal. The binder metal often includes cobalt (Co) and nickel (Ni) from the iron group metals, leading to the creation of various types such as tungsten-cobalt alloys, tungsten-nickel alloys, and tungsten-titanium-cobalt alloys, catering to the diverse performance requirements of different fields.
When tungsten is incorporated into steels, such as high-speed steels and certain hot-work mold steels, it significantly enhances the hardness and heat resistance of the steel, although at the cost of reduced toughness, highlighting the dual-edged sword nature of material performance optimization.
Lastly, it is imperative to mention that the primary application of tungsten resources lies in cemented carbides, commonly known as Tungsten Carbide. Cemented carbides, hailed as the “teeth” of modern industry, boast an extensive range of applications, with Tungsten Carbide components playing an irreplaceable role in numerous sectors due to their superior performance.